Unlocking Precision: How Small CNC Machines Drive Efficiency in Manufacturing
In the rapidly evolving landscape of modern manufacturing, the advent of Small CNC Machines has revolutionized how businesses approach precision engineering. According to a report by MarketsandMarkets, the CNC machine market is projected to reach $117.2 billion by 2027, with small machines playing a significant role in this growth due to their versatility and efficiency. These compact yet powerful machines are not only cost-effective solutions for small to medium-sized enterprises but also enhance production capabilities by offering high accuracy in machining operations, thus reducing material waste and improving process optimization.
Moreover, a study by TechNavio highlights that adoption of small CNC machines can lead to a staggering increase in production efficiency, estimated at over 30% in various manufacturing sectors. As industries strive to meet the demanding requirements of customization and faster turnaround times, the importance of Small CNC Machines cannot be overstated. They empower manufacturers to unlock precision in their operations, making it feasible to handle complex designs while maintaining a leaner operational footprint. This blog will delve deeper into how these machines are driving efficiency in manufacturing and reshaping the competitive landscape.
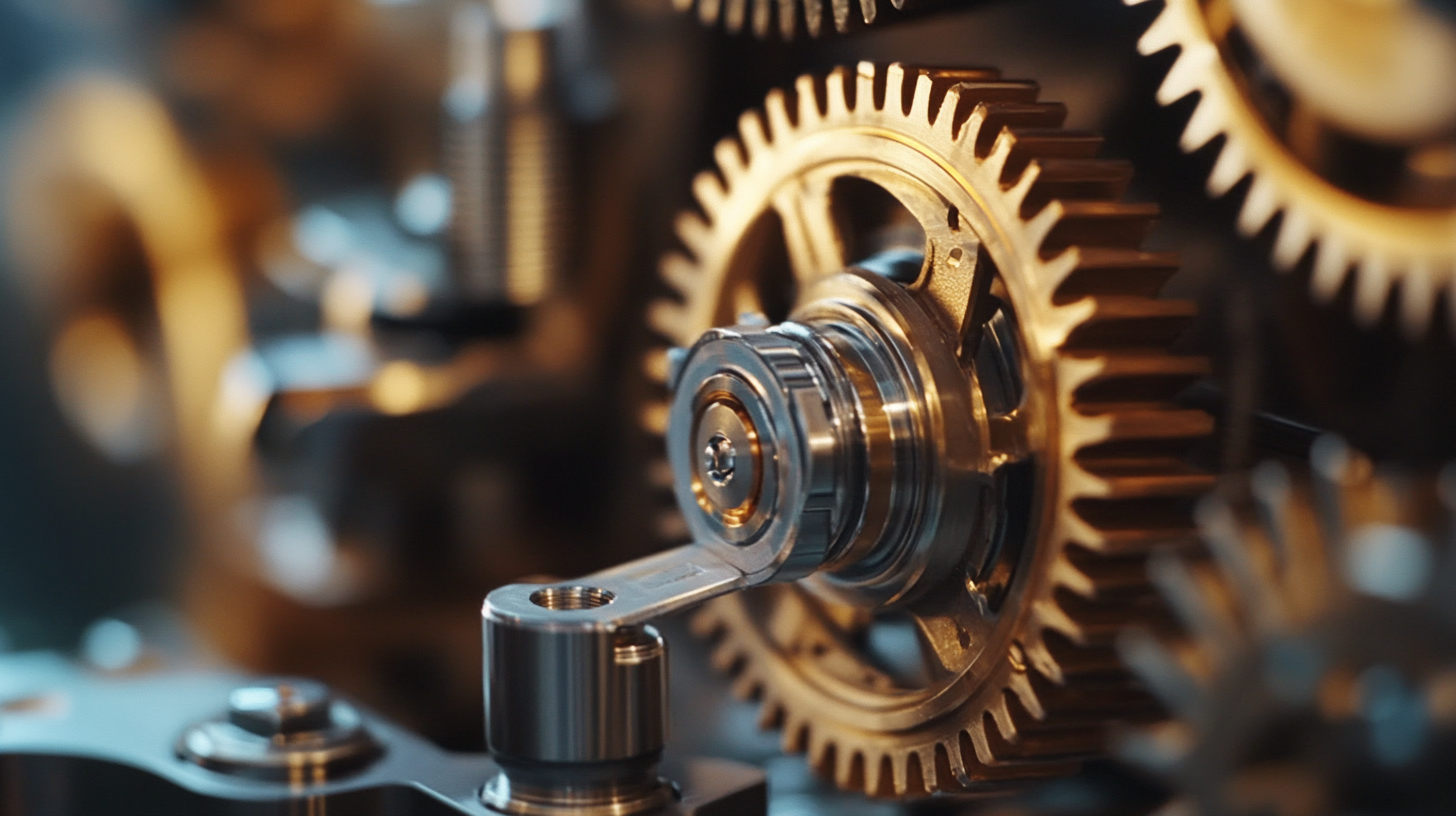
The Evolution of CNC Technology in Manufacturing Efficiency
The manufacturing landscape is undergoing a revolutionary transformation, primarily driven by advancements in CNC (Computer Numerical Control) technology. As manufacturers seek to enhance efficiency and precision, the evolution of CNC machines has become paramount. With a projected market size of US$ 162.16 billion by 2032, fueled by demand for automation and precision, CNC machining is at the forefront of this industrial shift. The rise of smart automation technologies, alongside the implementation of AI and IoT, is revolutionizing traditional manufacturing processes. Modern CNC machines, equipped with advanced computing capabilities, improve not only operational efficiency but also increase the accuracy of complex tasks. This evolution is crucial for industries that require high-precision parts, such as aerospace, automotive, and healthcare. As manufacturers integrate AI to analyze production data and make real-time adjustments, the outcome is a streamlined process that minimizes waste and maximizes productivity. Looking ahead, the implementation of multi-axis machining centers and next-gen CNC technology promises to further enhance operational capabilities. This development signals a new era where traditional manufacturing paradigms are reshaped, enabling businesses to respond swiftly to market demands while maintaining the highest standards of precision. Overall, the transformation brought about by CNC technology continues to foster a manufacturing environment that prioritizes efficiency and innovation.
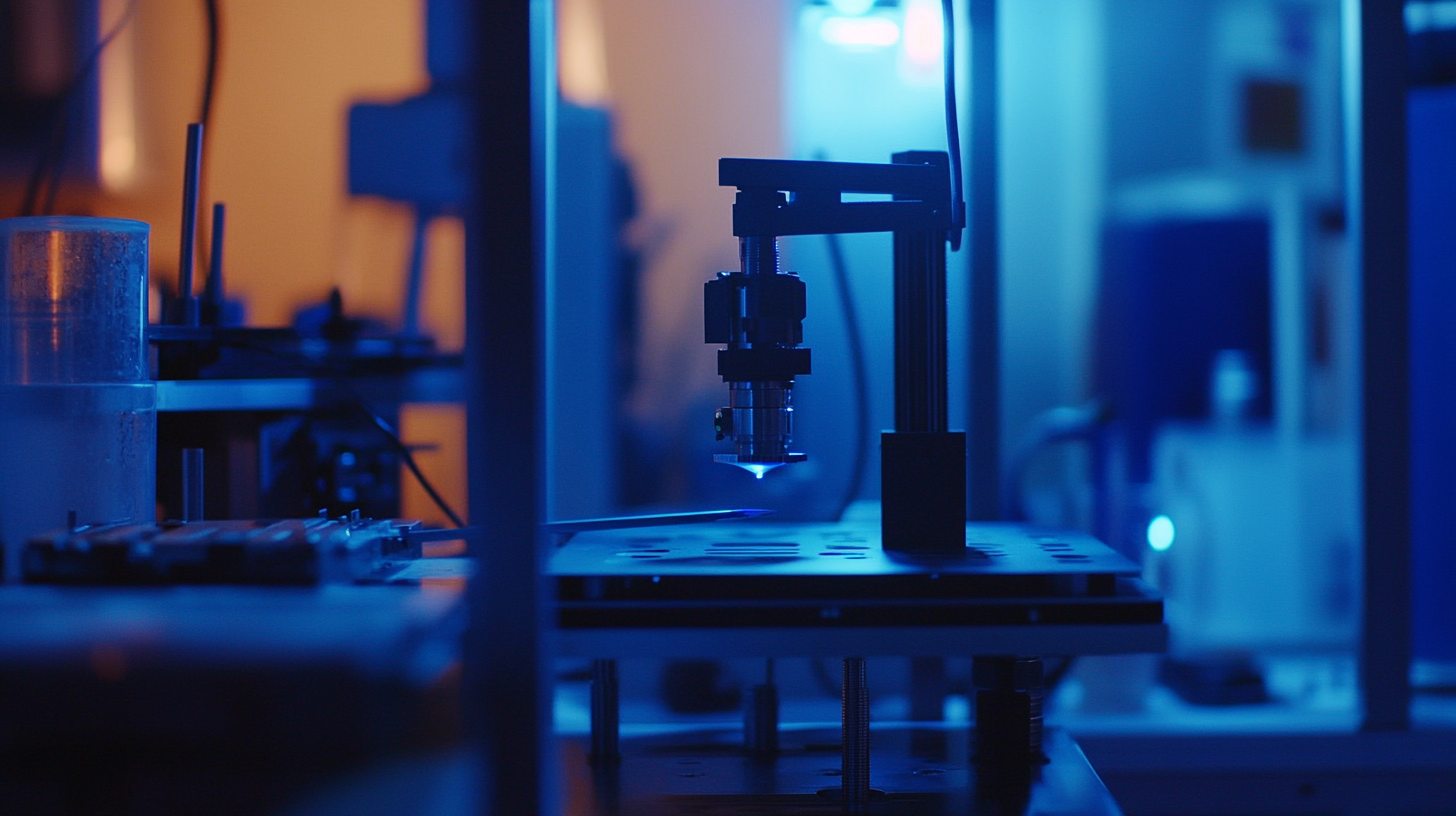
The Key Advantages of Small CNC Machines Over Traditional Methods
Small CNC machines are revolutionizing the manufacturing landscape, particularly when compared to traditional methods. One of the key advantages is their ability to deliver high precision with reduced material waste. According to a recent report by Guangfa Securities, the cost-effectiveness of small CNC machines can be significant, as they utilize advanced technology to optimize the production process, resulting in a decrease in manufacturing costs by up to 20% compared to conventional machining methods, which often involve higher labor and material costs.
Moreover, small CNC machines enhance flexibility and efficiency in manufacturing. With the ability to quickly switch between tasks and processes, these machines can accommodate a range of production demands without the lengthy setup times typically associated with traditional methods. This adaptability is especially valuable in industries where customization and short production runs are increasingly in demand. The same Guangfa Securities report highlights that businesses leveraging small CNC technology have reduced lead times by up to 30%, allowing them to respond more swiftly to market changes and consumer needs.
Additionally, the integration of AI and automation technologies into small CNC machines is furthering their efficiency and performance. These advancements enable manufacturers to achieve greater accuracy and consistency, minimizing the risk of errors that are more prevalent in manual methods. As reported, the ability to integrate AI into cost assessments for manufacturing processes, such as in the metal 3D printing sector, illustrates the evolving dynamics of CNC machining, emphasizing the growing importance of technology in enhancing operational effectiveness.
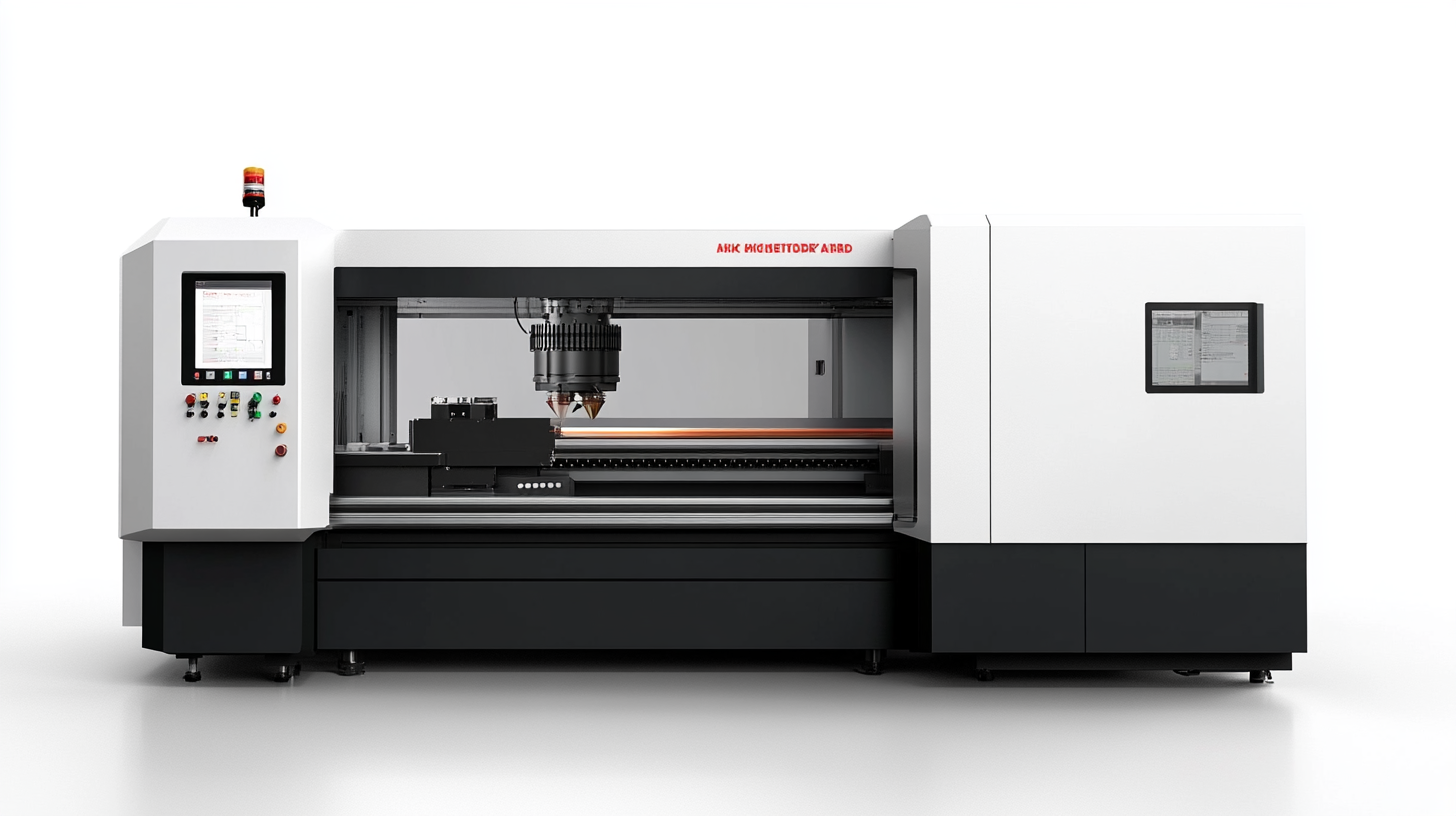
Applications of Small CNC Machines Across Various Industries
Small CNC machines have become integral to a multitude of industries, providing the precision and efficiency that modern manufacturing demands. Their applications span across sectors such as aerospace, automotive, and electronics, where meticulous machining and tailored components are essential. For instance, in the aerospace industry, small CNC machines are employed to create intricate parts that meet strict safety and performance standards, contributing to the overall reliability of aircraft. Similarly, in electronics, these machines are used to manufacture precise circuit boards and enclosures, ensuring high functionality and inventiveness in product designs.
The rising demand for automation and precision cutting has spurred growth in the CNC machine market, particularly for small CNC routers. As industries adopt advanced manufacturing techniques, these compact machines offer the versatility to handle both high-mix, low-volume production and more specialized tasks. This adaptability allows manufacturers to remain resilient in an ever-changing market environment while minimizing waste and maximizing output efficiency. The ongoing evolution in CNC technology, such as the integration of robotics and AI, further enhances the capabilities of small CNC machines, making them essential tools in achieving operational excellence.
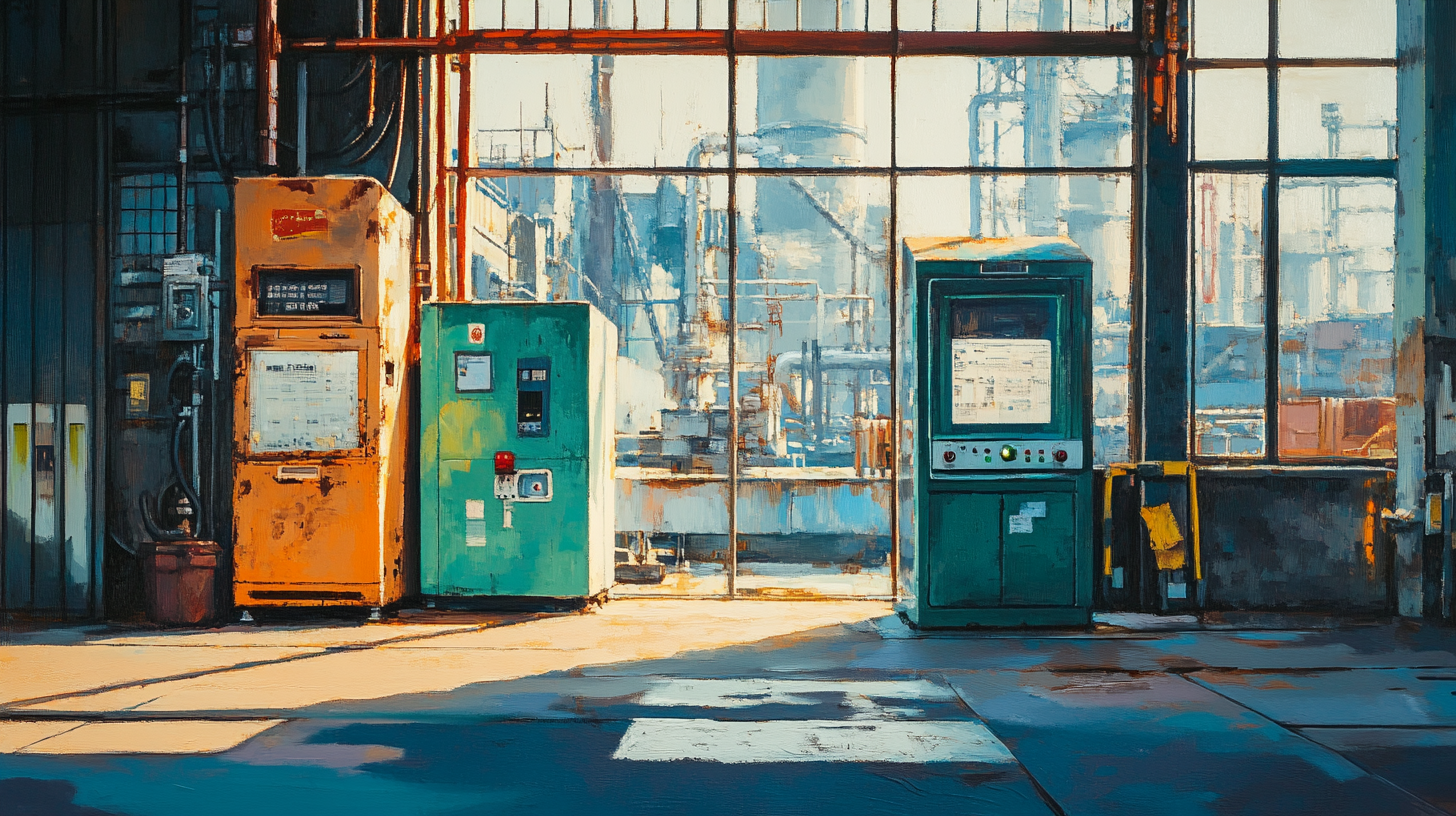
Boosting Production Speed and Accuracy with Small CNC Systems
Small CNC machines are revolutionizing the manufacturing landscape by significantly boosting production speed and accuracy. As industries worldwide continue to lean toward automation, these compact and versatile systems play a pivotal role in efficiently producing intricate parts with minimal waste. Their ability to perform complex machining tasks at high speeds allows manufacturers to meet the increasing demand for precision while maintaining cost-effectiveness.
The surge in the global CNC machine market, projected to reach $195.59 billion by 2032, illustrates the growing reliance on these technologies. The integration of advanced features, such as robotic automation, in small CNC systems is further enhancing productivity by facilitating quicker tool changes and improving material handling processes. As a result, businesses are not only enhancing their operational capabilities but also positioning themselves to adapt to the dynamic needs of various industries, including medical device manufacturing, where precision is paramount.
Furthermore, the impact of AI on CNC systems cannot be overlooked. As artificial intelligence continues to redefine manufacturing processes, small CNC machines are evolving to incorporate smarter controls that enhance their operational efficiency and flexibility. This blend of precision machining with intelligent technology paves the way for a new era in manufacturing, characterized by speed, accuracy, and adaptability to changing market trends.
Future Trends: Innovative Developments in Small CNC Machine Technology
The landscape of small CNC machine technology is rapidly evolving, with significant implications for the manufacturing sector. As we move into the future, innovative developments in small CNC machines are set to drive efficiency and precision like never before. The global CNC machine market, projected to grow from $101.22 billion in 2025 to $195.59 billion by 2032, reflects a compound annual growth rate (CAGR) of 9.9%. This robust growth highlights the increasing reliance on CNC machines, particularly in sectors that demand precision and flexibility.
Investments in research and development are crucial to advancing these technologies. Annual investments exceeding $3 billion in aerospace innovation are a testament to the industry’s commitment to enhancing manufacturing processes. This investment not only improves operational efficiency but also fosters the development of cutting-edge small CNC machines capable of meeting diverse needs in various sectors, including aerospace and defense.
Moreover, the precision machining market is also experiencing substantial growth. With an estimated size of $107.06 billion in 2023, the market is expected to expand at a CAGR of 7.8% from 2024 to 2030. This surge can be attributed to an aging population, which increases the demand for high-quality manufacturing solutions that enhance patient outcomes in healthcare, further underscoring the need for innovative small CNC machine technologies.