Innovative Approaches for Optimal Pipe Cutting Efficiency
In the manufacturing and construction industries, the efficiency of operations is paramount, particularly when it comes to processes like pipe cutting. According to a report by MarketsandMarkets, the global pipe cutting machine market is projected to reach $750 million by 2025, growing at a CAGR of 6.5%. This growth is driven by the increasing demand for automation and precision in pipe fabrication. As operational demands increase, the need for innovative approaches to enhance the performance of pipe cutting machines has never been more critical. Organizations that embrace these advanced solutions can significantly reduce waste and enhance productivity, leading to enhanced profit margins.
Innovative technologies such as laser cutting and water jet cutting are revolutionizing the capabilities of pipe cutting machines. Research from the American Society of Mechanical Engineers (ASME) indicates that precision cutting technologies can improve cutting speeds by up to 30% compared to traditional methods. Furthermore, the integration of digital tools and IoT devices in pipe cutting processes is yielding valuable data insights that enable real-time adjustments, optimizing efficiency and minimizing downtime. As the industry continues to evolve, companies that leverage these innovations in their pipe cutting operations will not only stay competitive but also set benchmarks in operational excellence.
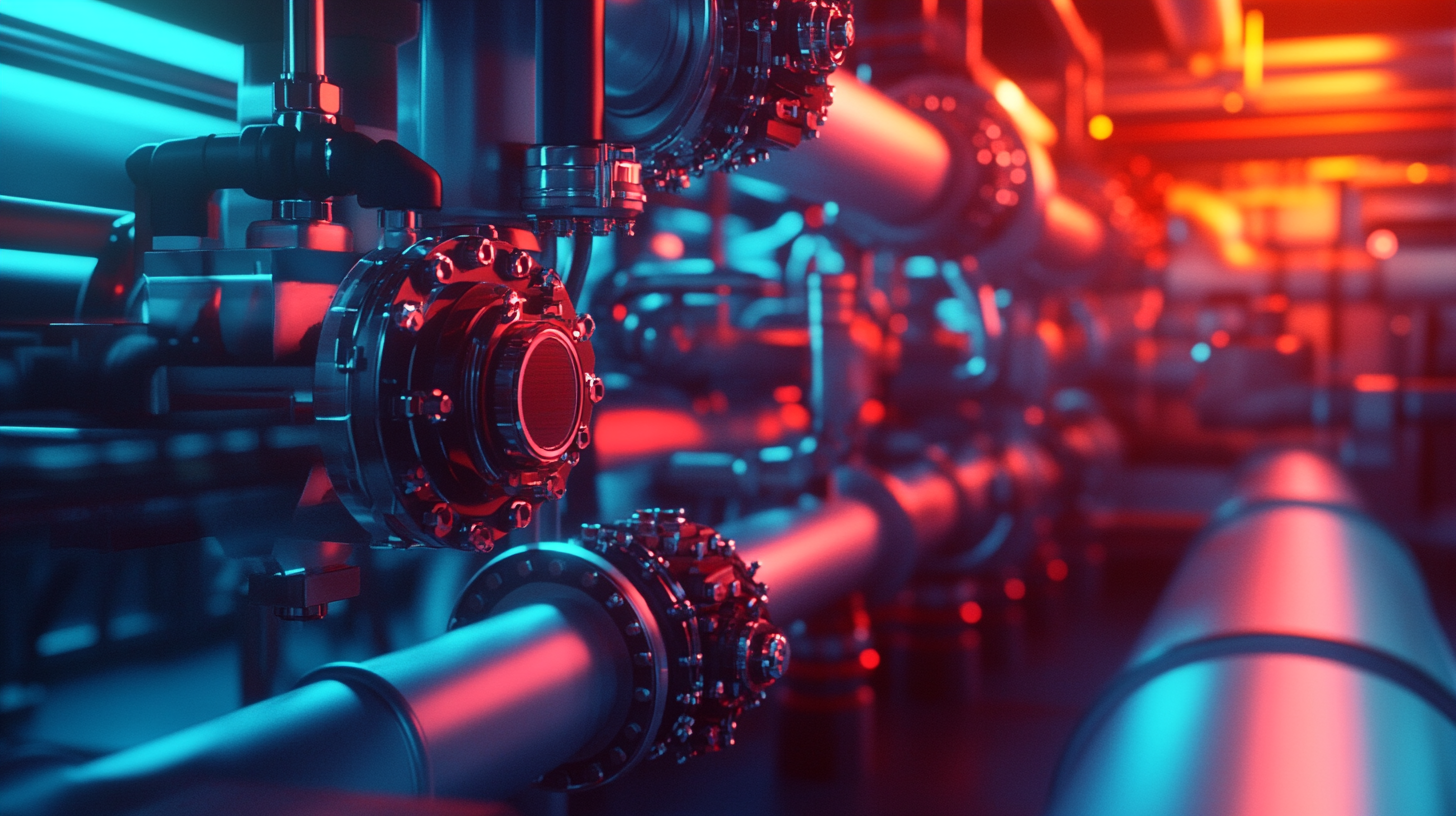
Revolutionizing Pipe Cutting: Advanced Techniques and Technologies
Revolutionizing pipe cutting has become essential in today's fast-paced industrial environment, where efficiency and precision are paramount. Advanced techniques and technologies are emerging to streamline the pipe cutting process, ultimately enhancing productivity and reducing waste. Automated systems integrated with sophisticated software are now capable of optimizing cutting paths, ensuring minimal material loss while maintaining high accuracy. These innovations not only save time but also significantly lower production costs. One of the standout advancements in pipe cutting technology is the use of smart robotics. These systems can adapt to various pipe sizes and materials, offering flexibility that traditional cutting methods lack. By utilizing machine learning algorithms, these robots continuously improve their cutting techniques based on real-time feedback, further enhancing efficiency. In addition to robotics, the introduction of advanced sensors and IoT connectivity allows for better monitoring of the cutting process and quality control, leading to improved outcomes and reduced downtime. Moreover, as industries move towards sustainability, eco-friendly practices are being integrated into pipe cutting processes. Technologies that minimize energy consumption and reduce carbon footprints are gaining traction. The adoption of cutting-edge materials that require less energy to cut is another step towards achieving sustainable manufacturing. As these innovative approaches continue to evolve, they promise to transform not just pipe cutting but the entire manufacturing landscape, paving the way for a more efficient and green future.
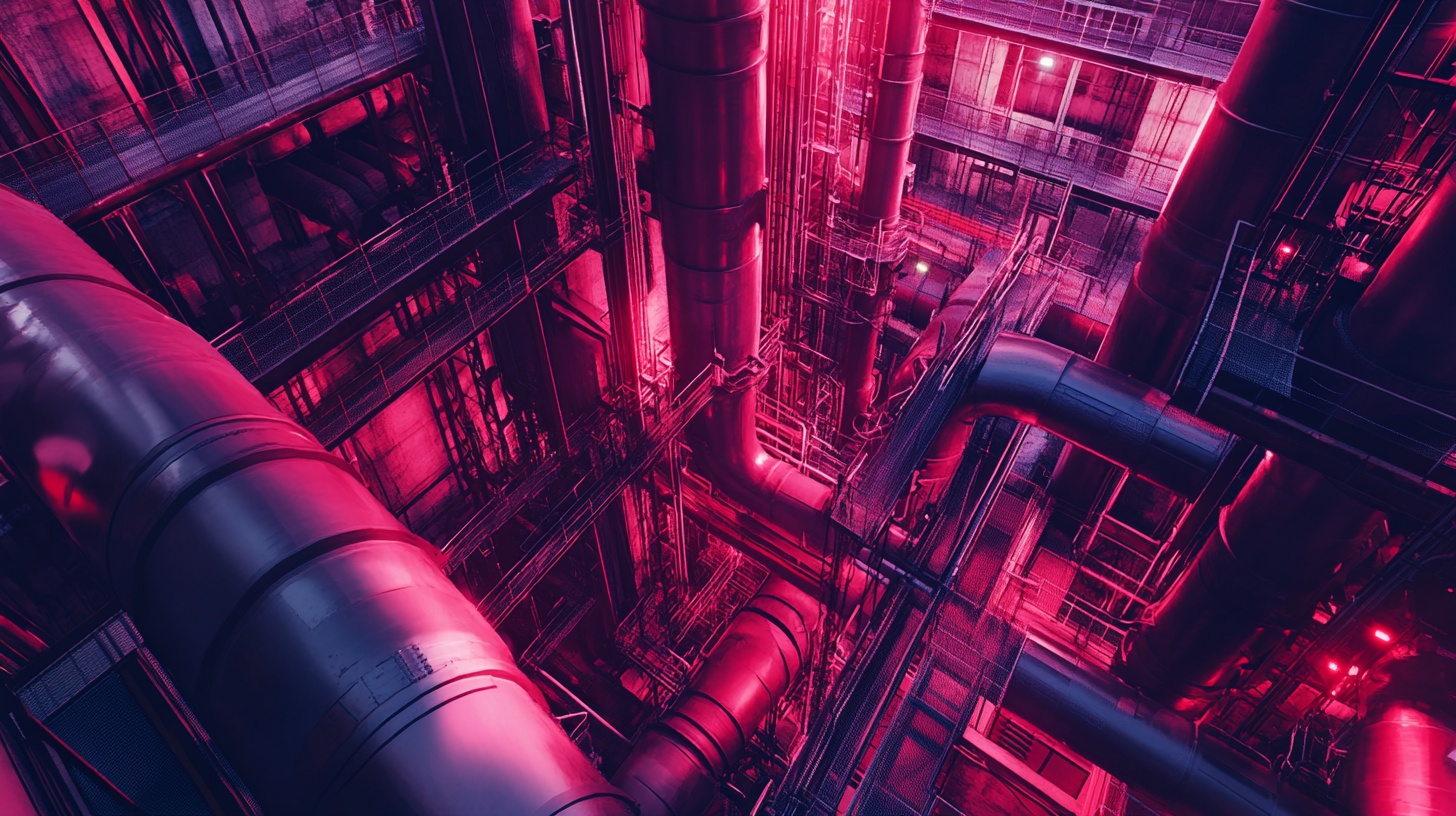
Maximizing Precision: The Role of Automated Pipe Cutting Systems
In the rapidly evolving landscape of manufacturing, precision in pipe cutting has emerged as a critical factor for enhancing operational efficiency. Automated pipe cutting systems represent a significant advancement in this endeavor, offering unparalleled accuracy that traditional cutting methods often struggle to achieve. According to a recent report by Market Research Future, the global market for automated cutting systems is projected to reach $2.5 billion by 2025, highlighting a robust demand driven by industries seeking to optimize their manufacturing processes.
The role of automation extends beyond mere precision; it encompasses increased productivity and reduced operational costs. A study conducted by the Fabricators & Manufacturers Association found that companies integrating automated pipe cutting technologies experience an average decrease in production time by up to 30%. This efficiency gain not only accelerates project timelines but also enables manufacturers to allocate resources more effectively, thereby enhancing overall productivity.
Moreover, the integration of advanced technologies, such as artificial intelligence and machine learning in automated systems, further enhances cutting precision. For instance, systems equipped with AI can analyze material properties in real-time, adjusting cutting parameters to maintain optimal performance. This translates to less material wastage, with reports indicating that automated cutting can reduce scrap rates by as much as 25%. As industries continue to prioritize sustainability alongside efficiency, the adoption of automated pipe cutting systems is poised to become a vital ingredient in the recipe for success.
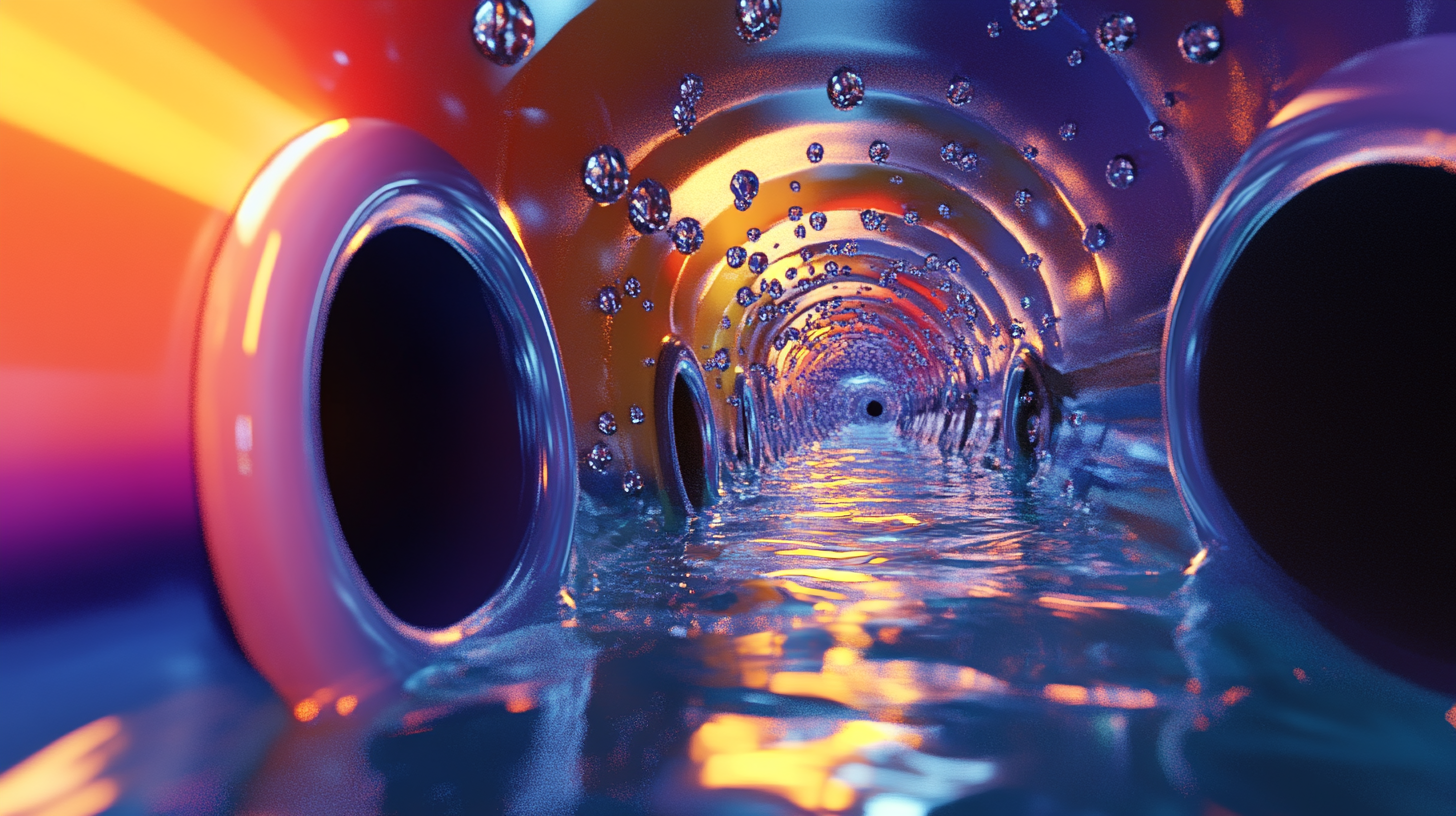
Eco-Friendly Practices in Pipe Cutting: Reducing Waste and Energy Consumption
In the modern manufacturing landscape, the push towards sustainability has led companies to explore eco-friendly practices in pipe cutting, which is traditionally a process known for high waste and energy consumption. According to a recent report by the International Energy Agency, the industrial sector accounts for approximately 35% of global energy use, with pipe production contributing a significant share of that figure. Adopting innovative cutting techniques can greatly reduce both energy consumption and material waste, benefiting the environment and the bottom line.
One effective method is the implementation of precision cutting technologies such as laser and waterjet cutting. These methods not only provide high accuracy, reducing the need for secondary machining processes, but they also minimize kerf loss—the amount of material wasted during cutting. Industry data indicates that precision cutting can reduce material waste by up to 30%, translating into substantial cost savings and lower environmental impact. Furthermore, by optimizing cutting paths and utilizing software that predicts material usage, manufacturers can further decrease waste and enhance efficiency.
In addition to direct cutting methods, recycling and reusing scrap materials is a crucial aspect of eco-friendly practices. A study from the Waste and Resources Action Programme (WRAP) highlights that recycling metals can save up to 95% energy compared to producing new materials. Companies that focus on reclaiming and repurposing off-cuts not only contribute to sustainability goals but also tap into new revenue streams, showcasing that environmentally responsible practices can align with economic advantages in the pipe cutting industry.
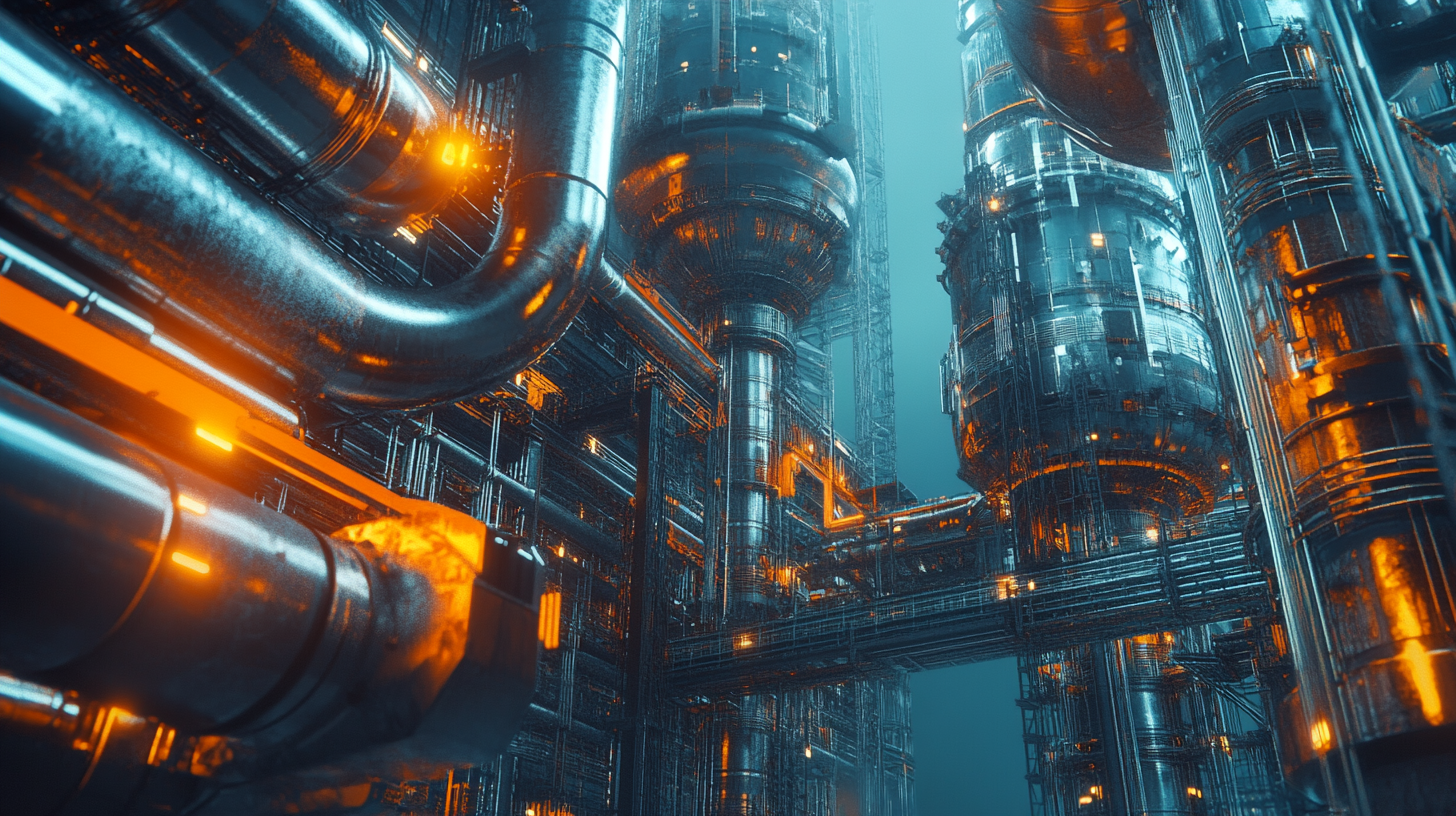
Integrating Smart Technology: The Future of Pipe Cutting Efficiency
As industries continue to evolve, the integration of smart technology is paramount for enhancing pipe cutting efficiency. In the oil and gas sector, companies are increasingly adopting digital transformation solutions that incorporate automation and electrification. These advancements not only streamline operations but also promote sustainable practices. By leveraging smart technologies such as IoT and machine learning, industries can optimize processes, reduce waste, and achieve greater precision in pipe cutting tasks.
The role of advanced technology in pipe cutting is becoming more evident as organizations like the Central Contra Costa County Sanitary District demonstrate significant gains by integrating inspection technology. This shift towards smart solutions enables better monitoring and management of resources, ensuring that operations are both efficient and sustainable. Techniques that utilize data analytics and real-time monitoring systems allow for timely decision-making, which is crucial in preventing downtime and minimizing material waste during cutting processes.
Looking towards the future, the concept of smart cities is emerging, where the integration of IoT, 5G connectivity, and advanced informatics revolutionizes construction and infrastructure projects. These cities prioritize technological advancements that enhance operational efficiency and resource management. As pipe cutting technology evolves, its alignment with these trends signifies a broader push towards sustainability and innovation in construction methods. The future of the industry lies in harnessing these smart technologies to create more efficient, agile, and environmentally conscious operations.
Training and Skill Development: Enhancing Workforce Efficiency in Pipe Cutting
In the ever-evolving world of pipe cutting, training and skill development play a pivotal role in enhancing workforce efficiency. As industries strive for greater productivity, investing in employee training programs specifically tailored for pipe cutting techniques can yield significant returns. By equipping workers with the latest skills and knowledge, companies can not only boost output but also enhance precision in their cutting processes.
One of the most effective approaches is the incorporation of hands-on training modules that simulate real-world scenarios. This allows workers to familiarize themselves with advanced cutting equipment and innovative technologies in a controlled environment before applying these skills on the job. Additionally, fostering an environment of continuous learning encourages employees to explore new techniques and strategies, further refining their abilities and increasing overall competency.
Furthermore, mentorship programs within organizations can bridge the gap between experienced and novice workers. Through personalized guidance, seasoned professionals can impart invaluable insights and practical skills, ensuring that essential knowledge is passed down. This not only enhances individual performance but also cultivates a strong team dynamic, resulting in improved collaborative efforts during complex cutting operations.