Essential Insights for Maximizing Efficiency with Cnc Plasma Cutters
In the ever-evolving world of manufacturing and metalworking, the importance of optimizing processes cannot be overstated. One of the most advanced tools at the disposal of fabricators today is the CNC plasma cutter. This innovative machine allows for precision cutting of various materials, resulting in clean, intricate designs that are crucial in a competitive marketplace. As technologies advance, understanding how to harness the full potential of a CNC plasma cutter becomes vital for businesses looking to enhance their production efficiency and overall output.
This blog aims to provide essential insights into maximizing the efficiency of CNC plasma cutters. Whether you're a seasoned professional or a newcomer to the field, recognizing the nuances of this technology can significantly impact your operations. From selecting the right materials and settings to maintenance tips and software integration, we will explore practical strategies that can lead to better results, quicker job turnarounds, and ultimately, a more profitable venture in the realm of CNC plasma cutting. Embrace the potential of this remarkable tool, and watch as your productivity soars.
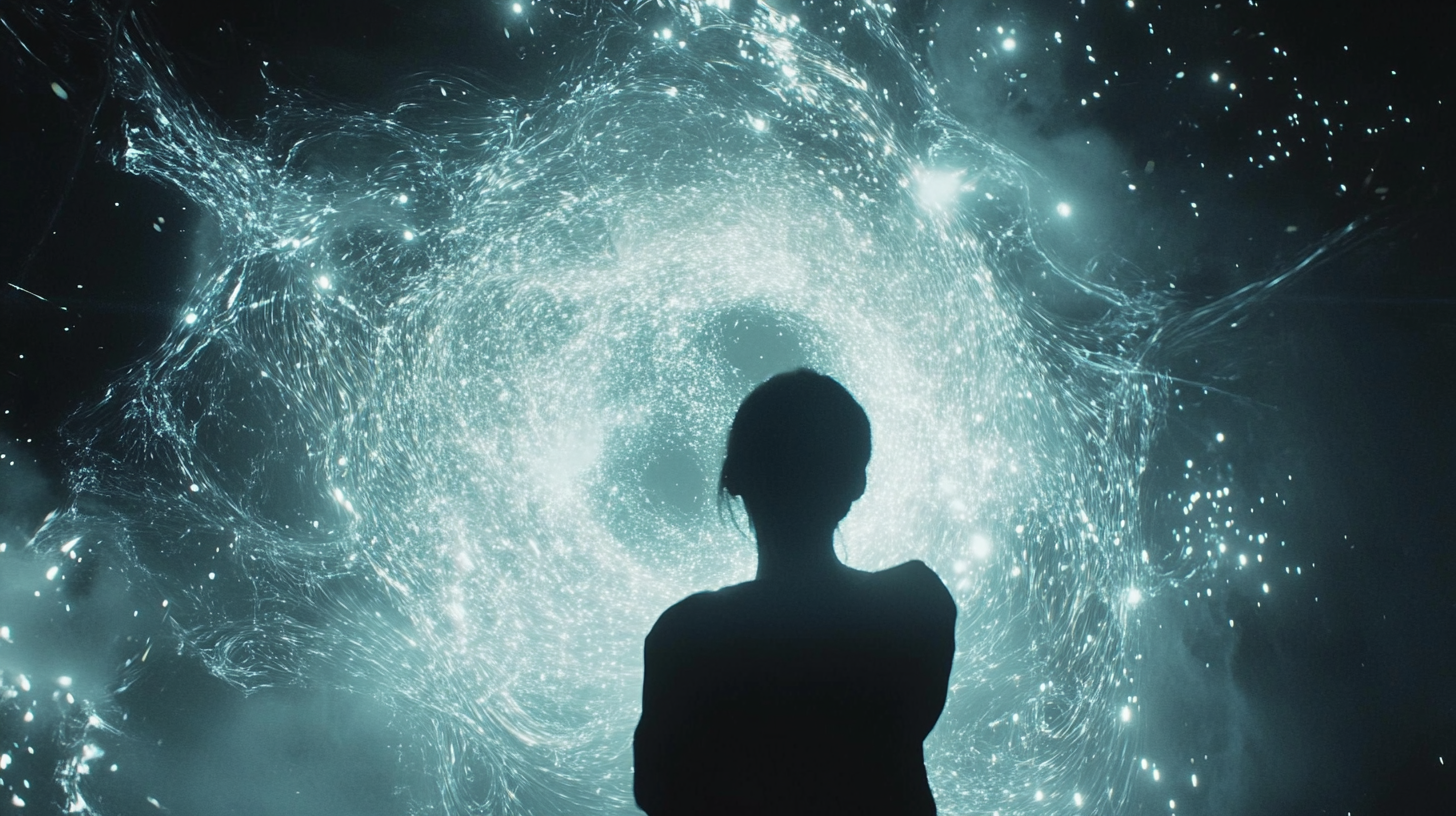
Understanding the Basics of CNC Plasma Cutting Technology
CNC plasma cutting technology has revolutionized the metal fabrication industry by providing precise and efficient cutting solutions. The core concept behind this technique involves using a high-velocity jet of ionized gas—plasma—to melt and blow away material from the workpiece. Understanding the fundamentals of this process is essential for anyone looking to harness the full potential of CNC plasma cutters. One of the critical aspects of CNC plasma cutting is its ability to cut through a variety of metals, including steel, aluminum, and copper, with great accuracy. The plasma arc reaches temperatures exceeding 20,000 degrees Celsius, allowing it to easily slice through thick materials while maintaining a clean edge. Furthermore, this technology is not limited to straight cuts; it can also handle intricate designs and shapes, making it a versatile tool in any workshop. Another important element of CNC plasma cutting is the role of computer numerical control. By programming the cutter using CAD software, operators can design intricate patterns that the machine will execute with precision. This automation ensures consistency and reduces the risk of human error, ultimately enhancing productivity. Additionally, CNC plasma cutters can be paired with different torches and settings based on the material and thickness, allowing for customized cutting experiences tailored to specific project needs.
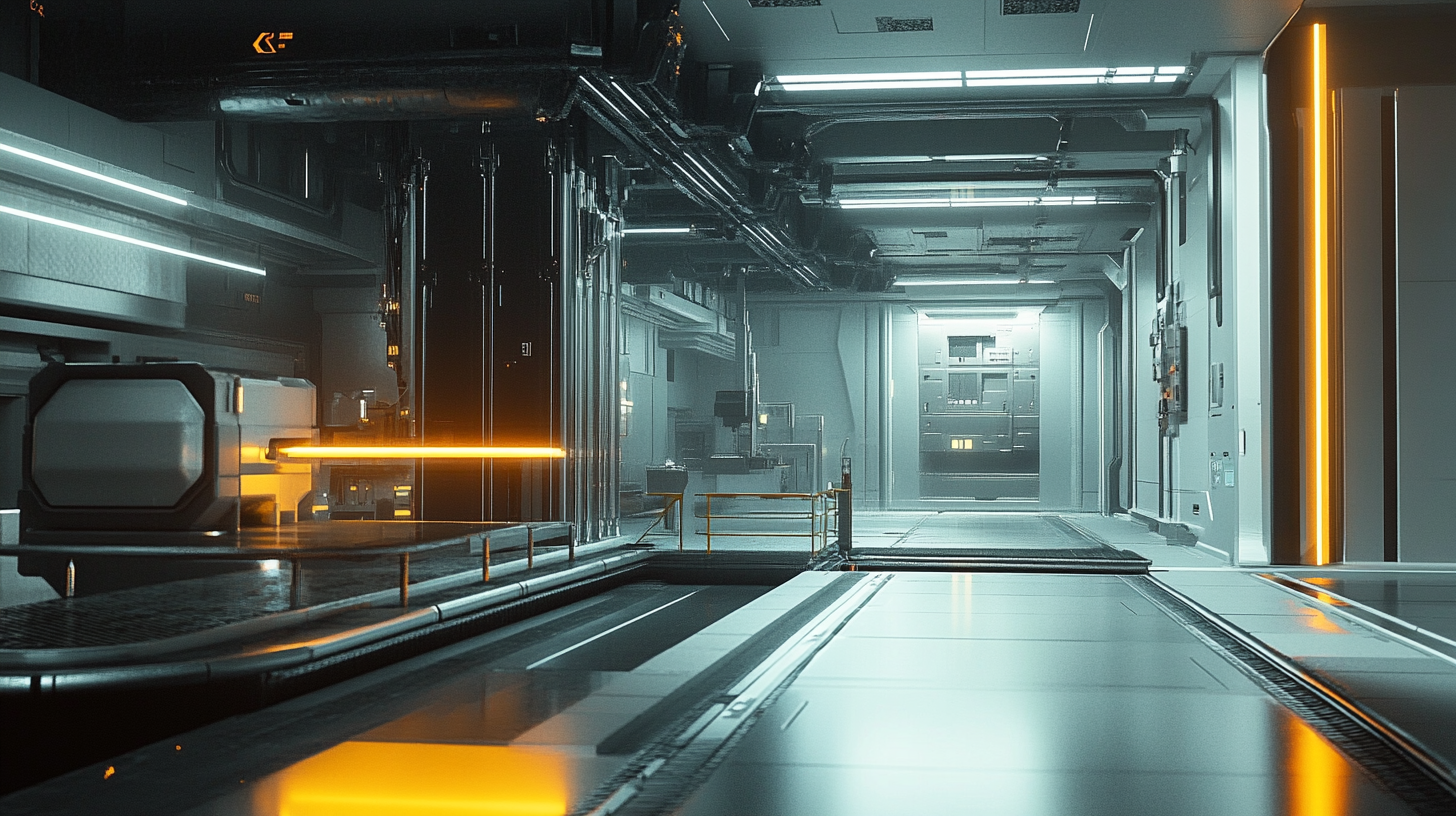
Key Factors to Optimize CNC Plasma Cutter Performance
When it comes to maximizing the efficiency of CNC plasma cutters, understanding the key factors that influence their performance is essential. One critical element is the optimization of process parameters, which can significantly affect the quality of the cut and the overall productivity. Variables such as cutting speed, gas flow rate, and arc voltage need to be carefully calibrated to achieve the desired outcomes. Fine-tuning these parameters not only minimizes material waste but also enhances the lifespan of the cutting equipment.
In particular, the challenge of cutting nickel-based superalloys like Inconel 718 demands specific attention. These materials, known for their strength and ability to withstand high temperatures, require precise settings to prevent issues such as excessive wear on the cutting tools or poor edge quality. Research into optimizing plasma arc cutting parameters for these alloys reveals that adjusting the heat input and controlling the cooling rate can lead to improved cutting efficiency and better overall results.
Another innovative approach to enhance CNC plasma cutting is the incorporation of advanced materials in cutting tools, such as carbon nanotubes (CNTs). By integrating CNTs, the mechanical properties of cutting tools can be significantly improved, leading to enhanced wear resistance and durability. As industries increasingly rely on high-performance cutting techniques, exploring these technological advancements will be critical for maintaining competitiveness and achieving superior machining results.
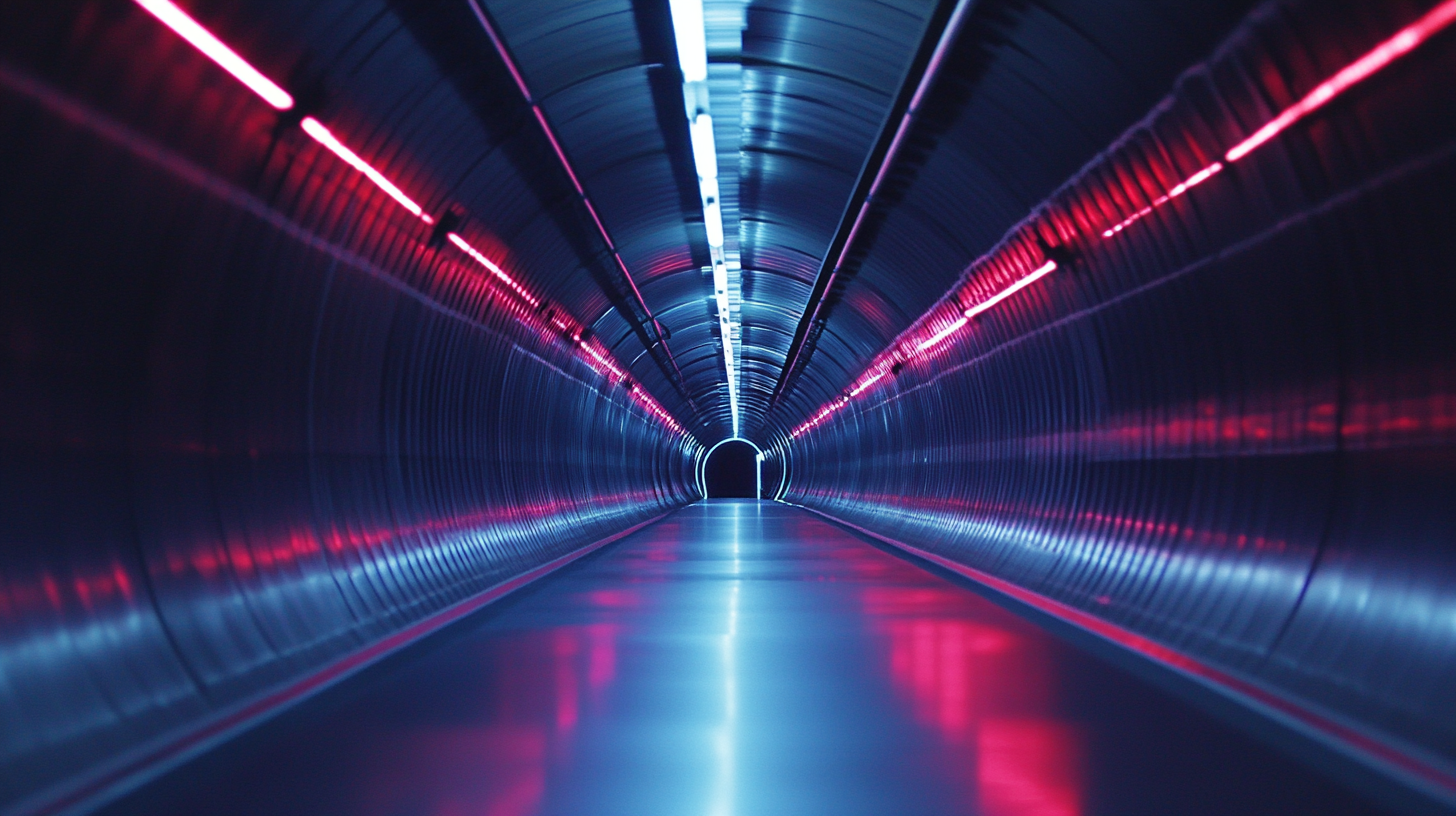
Common Mistakes to Avoid for Enhanced Cutting Efficiency
In the realm of CNC plasma cutting, understanding and avoiding common mistakes can significantly enhance operational efficiency. A study conducted by the Fabricators & Manufacturers Association indicates that poor setup and programming decisions can lead to an estimated 20% increase in production costs. Therefore, meticulous attention to detail before initiating a project is essential. Ensuring proper calibration of cutting machines and thoroughly reviewing settings like voltage and speed can prevent errors that lead to waste.
One notable oversight often observed in the industry is rushing through the material selection process. According to a report from the American Institute of Steel Construction, choosing inappropriate materials can diminish cut quality and place undue strain on the equipment, ultimately resulting in higher maintenance costs and downtime. Additionally, failure to conduct regular maintenance checks can exacerbate inefficiencies. A routine assessment can prolong the lifespan of CNC plasma cutters, reducing the chances of costly operational disruptions.
Another significant area where operators can falter is in their cutting techniques. Research shows that employing a consistent cutting speed and maintaining a steady hand can lead to a 15% improvement in cut precision. Often, operators underestimate the impact of their techniques, leading to increased rework and wastage. Investing in training sessions to educate operators on best practices not only fosters a culture of efficiency but also empowers teams to maximize their productivity on the shop floor. By avoiding these common pitfalls, manufacturers can see a substantial boost in their cutting performance and overall workflow efficiency.
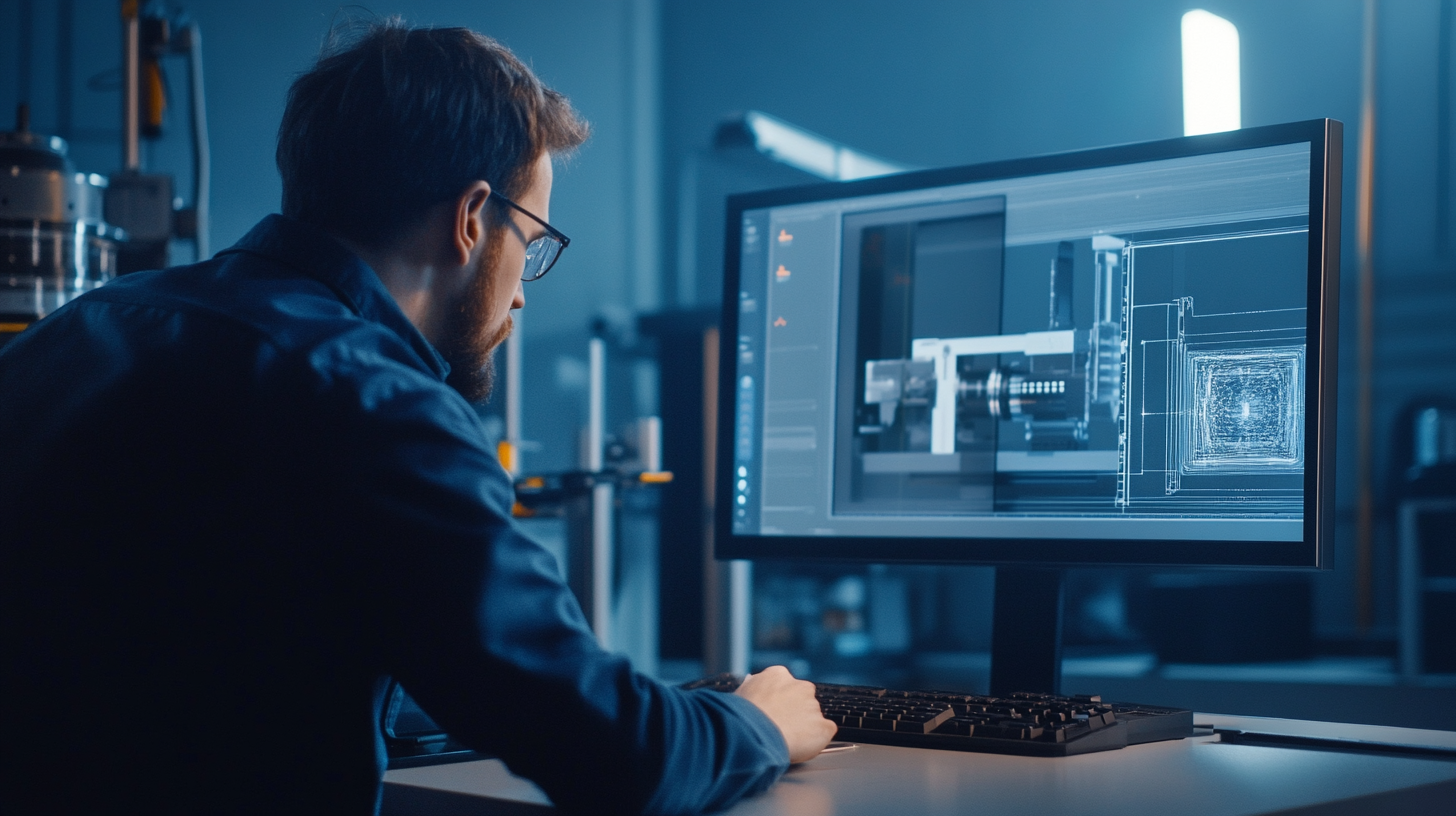
Essential Maintenance Tips for Long-Lasting CNC Plasma Cutters
Maintaining CNC plasma cutters is essential for ensuring their longevity and optimal performance. Regular maintenance not only extends the lifecycle of the equipment but also enhances cutting accuracy and reduces operational costs. According to a report by the Fabricators & Manufacturers Association, companies that implement a structured maintenance program can increase equipment efficiency by up to 25% and reduce downtime by as much as 50%. This emphasizes the importance of establishing a routine that includes thorough inspections and timely repairs.
One critical aspect of CNC plasma cutter maintenance is the inspection of consumable parts such as nozzles, electrodes, and shields. These components can experience wear and tear during operation, leading to compromised cut quality. The American Welding Society states that replacing worn consumables regularly can improve cut reliability and consistency, contributing to better overall productivity. Keeping a stock of spare parts on hand ensures that these replacements can be made swiftly, minimizing production interruptions.
Additionally, proper cleaning and lubrication of the machine's mechanical components should not be overlooked. Dust and debris can accumulate in the system, affecting both the precision of cuts and the efficiency of the machine. Regular cleaning, as outlined in the operational manual, combined with periodic lubrication, can significantly reduce friction and energy consumption. According to a study by the National Institute of Standards and Technology, well-maintained equipment can operate at 10%-15% lower energy levels compared to poorly maintained counterparts, translating into considerable cost savings over time.
Innovative Techniques for Advanced Plasma Cutting Applications
In the rapidly evolving landscape of advanced manufacturing, the integration of innovative techniques in CNC plasma cutting has emerged as a game changer. The recent annual conference held by the China Steel Structure Association highlighted the importance of such advancements, especially in the context of the cold-formed steel industry. As industries seek to streamline operations and enhance productivity, the application of cutting-edge plasma cutting technologies becomes pivotal.
One innovative technique gaining traction in advanced plasma cutting applications is the utilization of optimized software systems that enhance cutting path efficiency. By employing algorithms that account for material variations and specific project requirements, manufacturers can minimize waste and reduce cycle times significantly. Additionally, advancements in torch technology have led to more precise cuts, making it easier to achieve intricate designs that meet increasingly diversified customer needs.
Moreover, the forum discussions emphasized the significance of training skilled technicians in employing these advanced techniques. Individuals like Wang Baoquan, a senior technician recognized for his contributions in casting operations, exemplify the critical role of expertise in maximizing the potential of modern tools. As industries continue to embrace these innovative practices, the demand for proficient personnel who can operate sophisticated machinery will only increase, further driving the evolution of plasma cutting in manufacturing.