Unlocking Efficiency: Mastering the Use of Plate Laser Cutting Machines in Your Production Line
In today’s competitive manufacturing landscape, efficiency and precision are paramount. One of the most innovative tools revolutionizing production lines is the Plate Laser Cutting Machine. This advanced technology not only enhances the accuracy of cuts but also significantly reduces waste and operational time. By incorporating these machines into the production workflow, manufacturers can achieve remarkable improvements in productivity, establishing themselves as leaders in their respective industries.
As we explore the intricacies of mastering Plate Laser Cutting Machines, we will uncover the various techniques and best practices that can unlock their full potential. From optimizing settings for different materials to implementing effective maintenance strategies, understanding how to leverage these machines effectively is crucial for maximizing both output and quality. Join us as we delve into the world of laser cutting technology and discover how it can transform your production line into a beacon of efficiency and reliability.
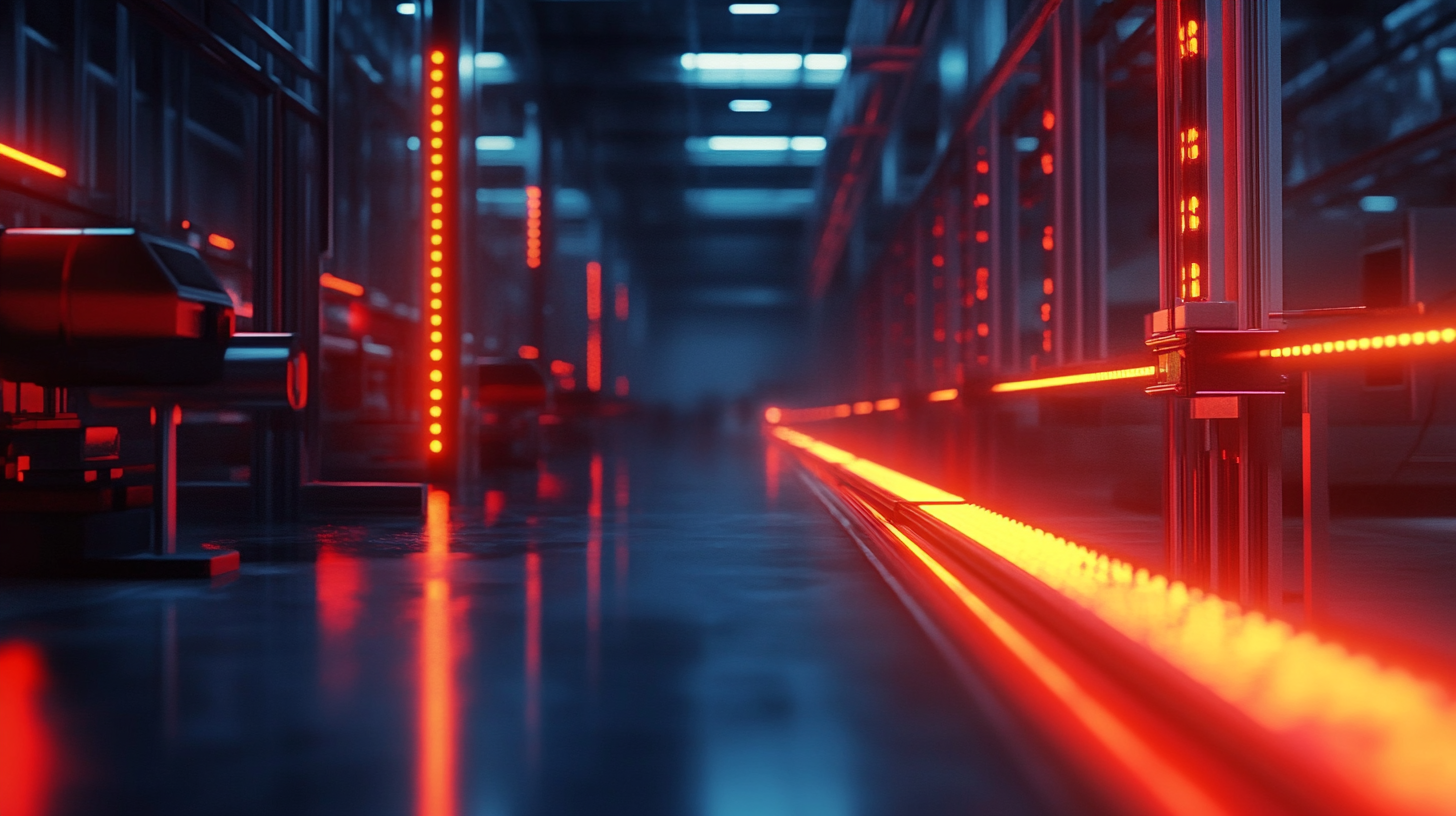
Understanding Plate Laser Cutting Technology and Its Benefits
Plate laser cutting technology represents a significant advancement in manufacturing processes, offering unprecedented precision and efficiency in cutting materials. This technology utilizes focused laser beams to slice through various thicknesses of plate metal with incredible accuracy. The high-intensity laser can create intricate designs and complex shapes that would be challenging to achieve with traditional cutting methods. As a result, businesses can produce components with tighter tolerances and enhanced surface finishes, ultimately improving the quality of the final products. One of the primary benefits of plate laser cutting lies in its ability to minimize waste. The precision of the laser allows for snug nesting of parts on the plate material, maximizing the use of raw materials. This not only reduces costs associated with material consumption but also contributes to more sustainable practices by lowering the amount of scrap generated during production. Moreover, laser cutting technology often requires less energy than conventional cutting methods, further enhancing its appeal in terms of both cost savings and environmental impact. In addition, the speed of plate laser cutting is a game changer for production lines. With the capability to rapidly cut and process multiple parts simultaneously, manufacturers can significantly shorten lead times and respond more quickly to market demands. The automation of laser cutting machines also minimizes the potential for human error, streamlining operations and freeing up skilled labor for more complex tasks. As industries continue to evolve towards faster and more efficient production methods, mastering plate laser cutting technology will be essential in maintaining a competitive edge.
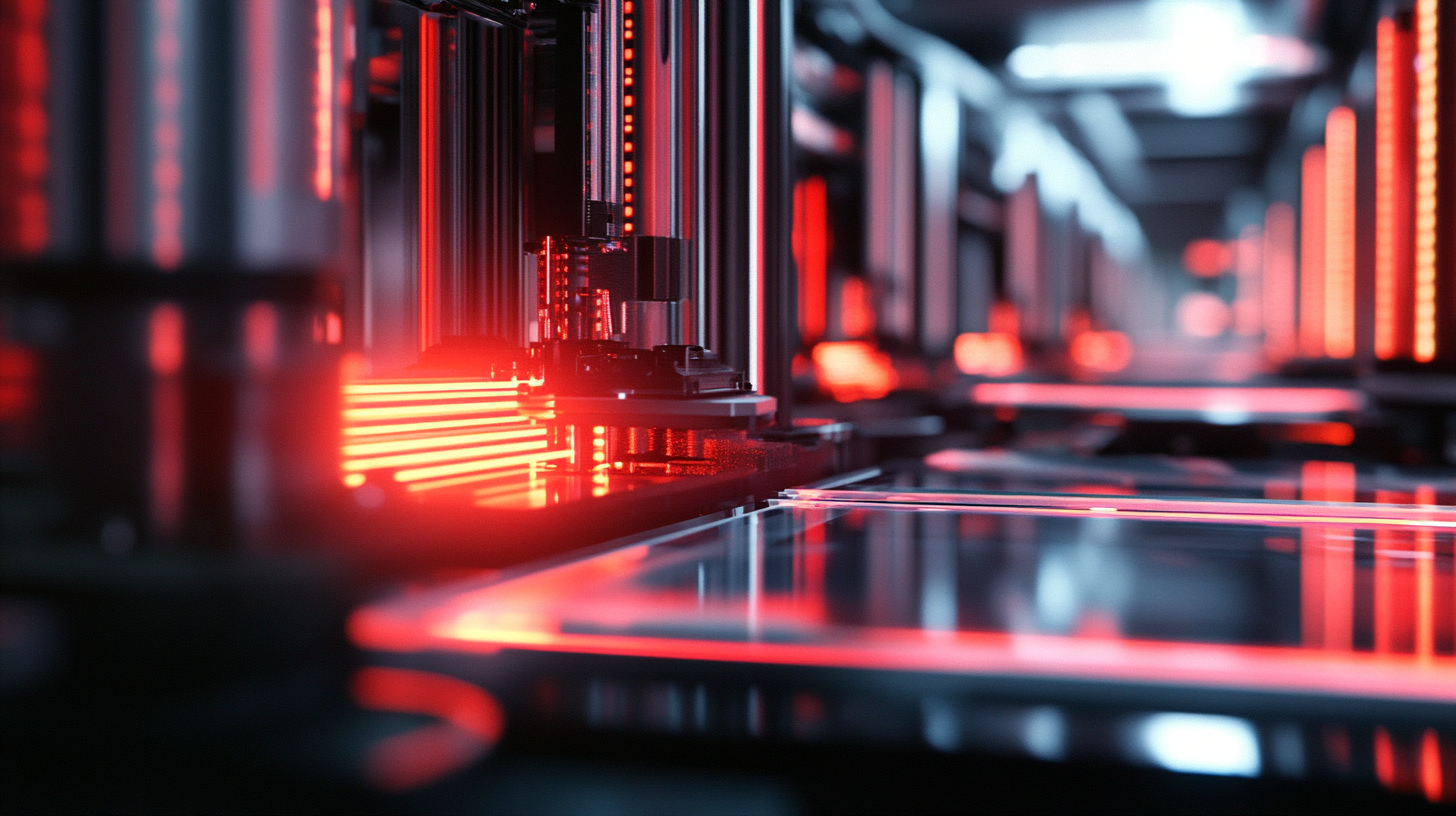
Key Factors in Choosing the Right Plate Laser Cutting Machine
When it comes to enhancing production efficiency, selecting the right plate laser cutting machine is critical. Industry reports indicate that laser cutting technology can improve production speed by up to 25% compared to traditional cutting methods. This increased efficiency can significantly reduce operational costs and lead times, making it an invaluable investment for manufacturers looking to stay competitive.
One of the key factors in choosing the right laser cutting machine is understanding the materials you plan to work with. According to a report by the Fabricators & Manufacturers Association (FMA), 70% of manufacturers found that the ability of a laser cutter to handle a variety of materials—including metals, plastics, and composites—was a determining factor in their purchasing decisions. Machines equipped with advanced features, such as fiber laser technology, provide the versatility needed to cut through thicker materials with precision.
Another crucial aspect is the machine's power and speed capabilities. Data from McKinsey & Company suggests that having a machine with a higher wattage can significantly influence both the cutting speed and the quality of the cuts. For instance, a 6kW fiber laser can cut through 20mm mild steel at a rate nearly twice that of a conventional 3kW machine. Therefore, evaluating your production demands alongside the specifications of the machinery can ensure you make an informed choice that boosts your overall productivity.
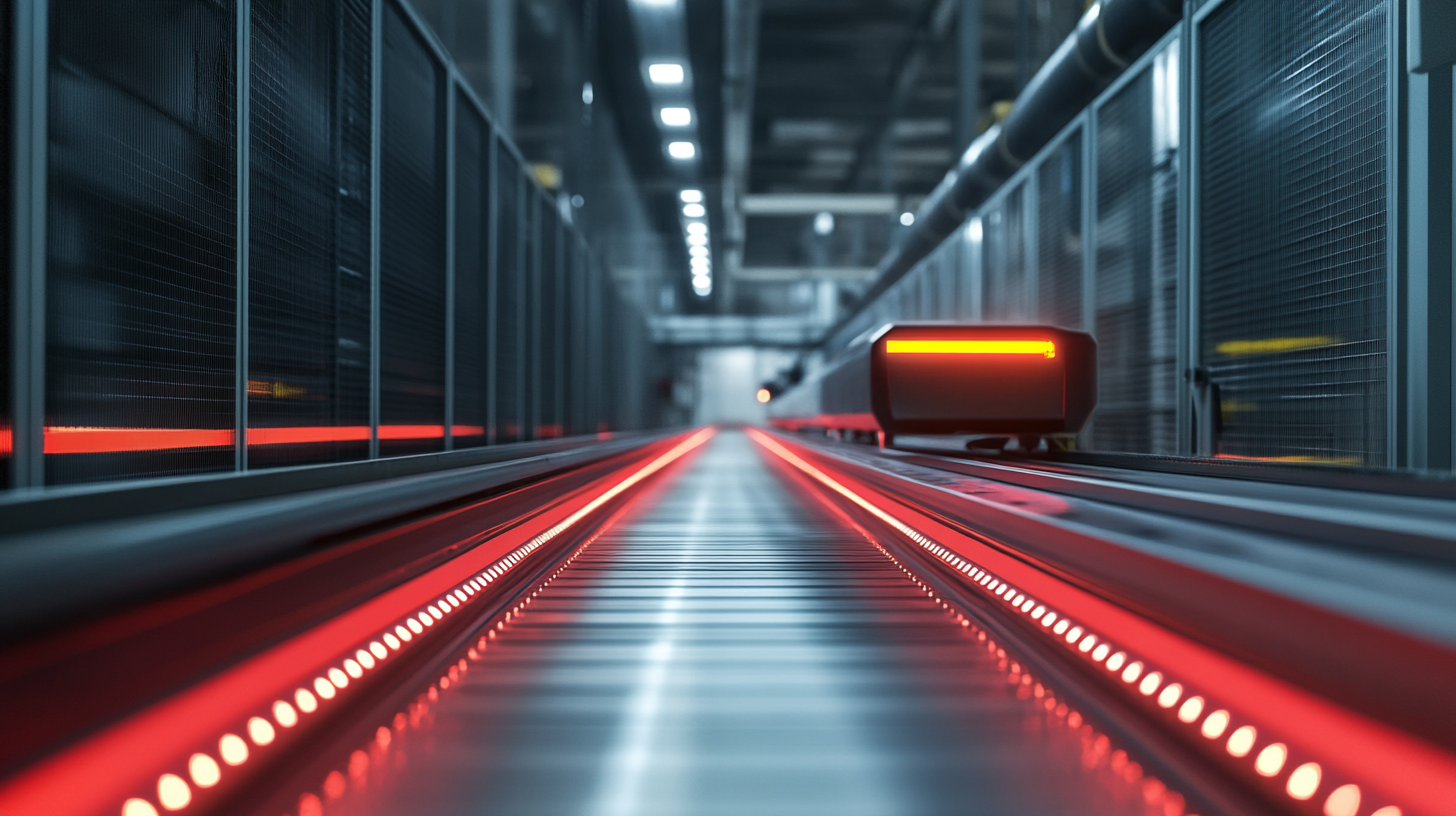
Integrating Plate Laser Cutters into Existing Production Workflows
Integrating plate laser cutters into existing production workflows can significantly enhance efficiency and precision in manufacturing processes. According to a report from the International Laser Manufacturing Research Center, the adoption of laser cutting technology has increased by 25% among manufacturers over the past five years, largely due to its ability to reduce waste and minimize operational costs. By seamlessly incorporating plate laser cutting machines, companies can streamline their operations, allowing for faster cycle times and improved product quality.
One of the key advantages of integrating plate laser cutters is the flexibility they offer. Unlike traditional cutting methods, laser cutting allows for intricate designs and the ability to easily switch between different materials, from metals to plastics. A study by MarketsandMarkets indicates that the global laser cutting market is expected to grow from $3.5 billion in 2020 to $5.8 billion by 2025, highlighting the increasing reliance on laser technology in various sectors. By embedding these machines into their production lines, manufacturers can enhance their capabilities and respond more swiftly to market demands.
Moreover, the integration process involves careful consideration of existing workflows to ensure compatibility and efficiency. Implementing advanced software solutions that can communicate with both the plate laser cutters and the existing machinery is essential for optimizing production processes. Research from Deloitte shows that companies that effectively integrate new technologies can increase their operational efficiency by up to 30%, thereby solidifying their competitive edge in the market. Recognizing the value of this integration will be crucial for companies aiming to remain at the forefront of their industries.
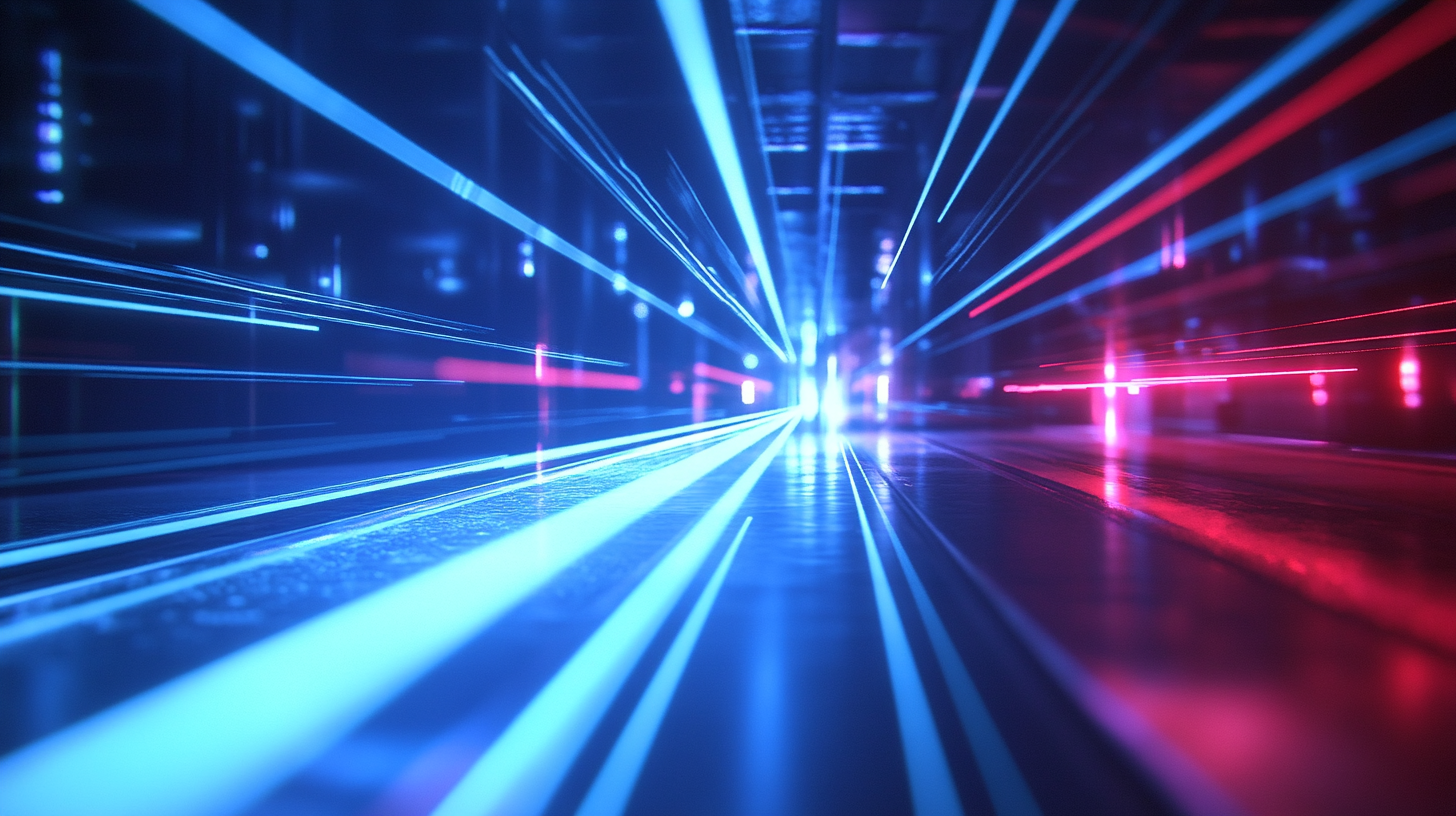
Best Practices for Maintaining and Optimizing Laser Cutting Machines
Maintaining and optimizing laser cutting machines is crucial for maximizing efficiency on your production line. One of the key best practices involves routine maintenance, which includes regular cleaning of the optics, checking for any signs of wear and tear on the components, and ensuring that the ventilation system is functioning properly. Keeping the lens and mirrors free of debris not only enhances cutting quality but also prolongs the lifespan of the machine. Scheduling maintenance during off-peak hours can minimize downtime, ensuring that production schedules remain on track.
Another vital aspect is the calibration of the machine. Regularly calibrating the laser cutting machine ensures precision in cuts, reducing material waste and rework. Operators should be trained to utilize software that monitors the laser's performance. This not only helps in identifying potential issues before they escalate but also facilitates adjustments to enhance cutting speed and accuracy. Learning how to interpret machine diagnostics can lead to timely interventions that optimize production efficiency.
Lastly, staying updated with the latest technologies and software enhancements is essential. Many modern laser cutting machines come equipped with advanced features that can significantly boost productivity. Training personnel to harness these technologies effectively can lead to notable improvements in the production process. By implementing these best practices, manufacturers can unlock the full potential of their laser cutting machines, leading to a more streamlined and efficient production line.
Future Trends in Plate Laser Cutting: Innovations to Watch Out For
The landscape of plate laser cutting technology is rapidly evolving, driven by the need for increased efficiency and precision in manufacturing processes. As highlighted in a recent report by Market Research Future, the global laser cutting market is projected to reach USD 5.8 billion by 2025, growing at a compound annual growth rate (CAGR) of 6.4%. This growth is spurred by innovations that are set to redefine operational capabilities in various sectors, from automotive to aerospace.
One notable trend is the integration of artificial intelligence and machine learning into laser cutting systems. These advancements enable machines to optimize cutting paths in real-time, significantly reducing wastage and downtime. A study by Deloitte indicates that companies adopting AI in their production lines can enhance their productivity by up to 30%. Furthermore, with the increasing emphasis on sustainability, manufacturers are turning to fiber laser technology, known for its energy efficiency and ability to cut a wider range of materials with minimal environmental impact.
Additionally, the advent of automation in plate laser cutting processes cannot be overlooked. Robotic arm integration allows for continuous operation, further enhancing production speed while maintaining high levels of accuracy. According to a report from Allied Market Research, the robotic laser cutting market is expected to expand at a CAGR of 9.2%, signifying a clear shift toward automated solutions that promise not only to boost output but also to improve workplace safety by reducing human intervention in potentially hazardous environments. As these trends unfold, staying ahead of the curve will be imperative for manufacturers seeking to thrive in an increasingly competitive market.