Challenges in Adopting Laser Cutting Technology for Global Buyers
The most rapid technological advancement, however, has become quite a modification to the manufacturing picture-from laser cutting-a significant precision and efficiency method. Global buyers who run with plans of such technologically advanced operations may face many obstacles that would block them from such smooth adoption of laser cutting. These hurdles would need to be well understood by any party in search of benefits from laser cutting since they would have varied forms ranging from a large initial investment cost with specialized training to fears of maintenance and good sourcing of materials.
Not only this, but complex also effort is integrating laser cutting technology to existing production processes because the varying quality standards International regulations and fast developing pace of technology complicate the process. While the global buyers will face these challenges, strategies should be put in place to address the very complaints to the buyers and at the same time maximize laser cutting as a game-changing solution in manufacturing. In this blog, the main challenges identified are global buyers adopting laser cutting technology and solutions to overcoming these challenges effectively.
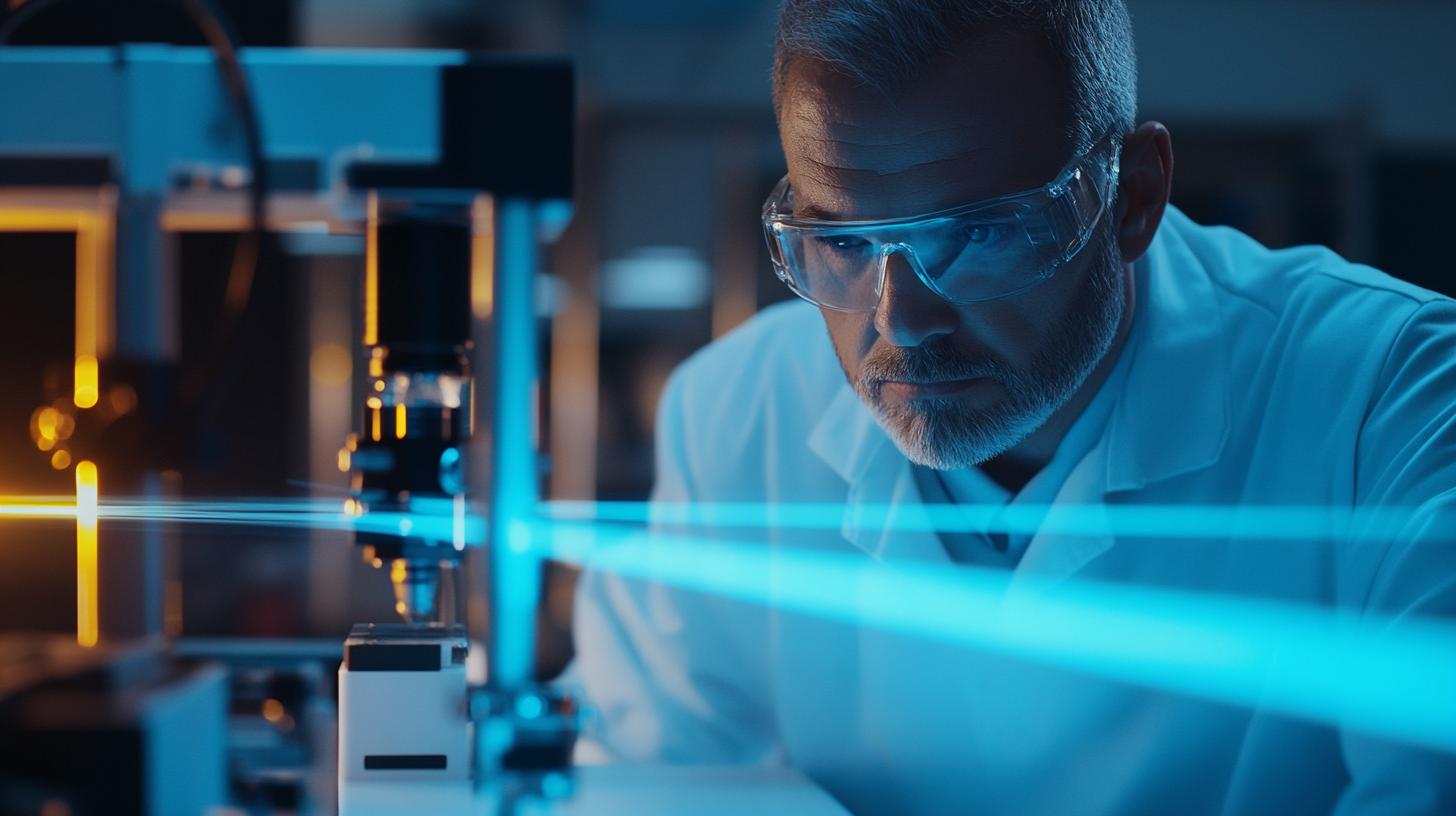
Understanding the Initial Investment and Cost Implications of Laser Cutting Technology
Now, the present scenario of laser cutting technology for the global buyer poses numerous problems as well as opportunities. The advanced manufacturing methods are being sought out largely by industries where an understanding of the initial investments plus cost implications is critical. A recent report by the People's Daily about increasing manufacturing investment in Shandong analyses the cloud of excitement surrounding labour-saving technologies. This broader picture, where the first-quarter growth of 25.1% attests to high-tech manufacturing sectors outpacing the traditional, seemingly augurs well for the feasibility and probable return on any investment made on laser cutting technology. HSG Laser's establishment of a manufacturing base in Thailand therefore gives a strategic blessing to laser technology internationalization. This factory is to utilize the manufacturing potentials of the region, while at the same time offering advanced solutions to the markets nearby. Global buyers considering the adoption of laser cutting technology may feel intuitively frightened by the initial costs. This investment, however, will quickly fade away in importance as benefits arise from operational efficiency and reductions in operational costs. The market for laser cutting applications, growing as it is, ought to compel careful scrutiny of these costs in relation to production goals among buyers competing in an increasingly aggressive environment. In addition, advances in laser technology are being increasingly deemed important in the semiconductor industry, evident from the recent funding attained by Crystal Fly Semiconductor. Thereby, this situation indicates how laser advancements are conceived as critical catalysts for industrial transformation, dovetailing with investments toward high-tech. Buyers, on an international scale, will have their focus on aligning such investments with grander goals of digitalization and automation.
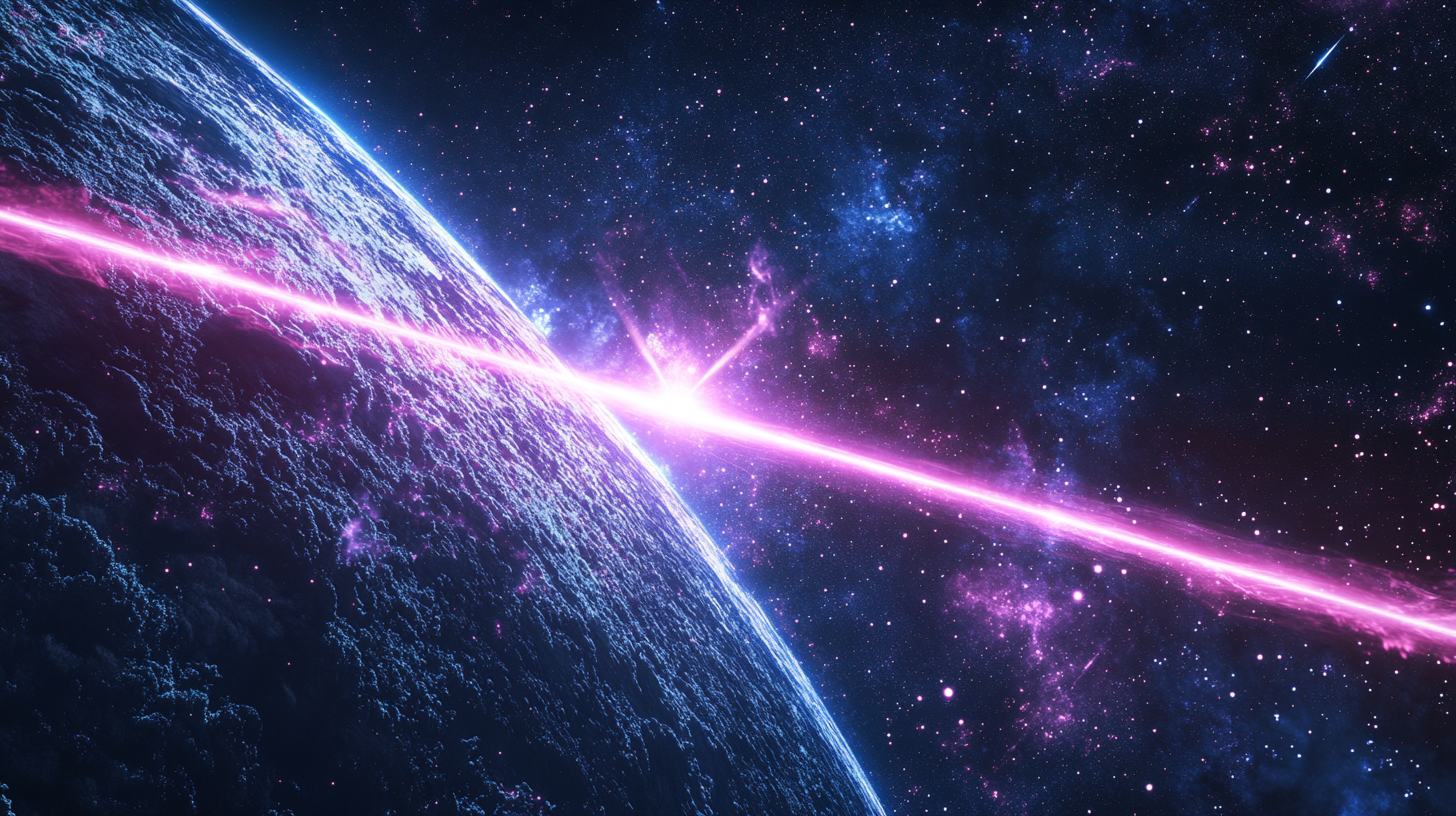
Evaluating Technical Expertise and Training Requirements for Global Buyers
The global buyers have to face considerable problems accepting laser cutting technology for evaluating technical expertise and the training requirements it entails. The demand for precision cutting tools, especially lasers, has increased dramatically with the rapid transformation in industries. Unfortunately, the gap is usually left open for prospective users due to the high level of knowledge and skills required for operating this highly sophisticated technology.
The assessment of current levels of technical expertise in their workforces is crucial for many companies, particularly new entrants into the laser cutting market. It gives them an upper hand in identifying specific areas that require extra training. Such prospective users will have to consider whether their workforce possesses the underlying basics in optics and materials science as well as machining principles to capitalize fully on laser cutting technology. This self-assessment can be the most significant initial step towards bridging the knowledge gap prior to transitioning toward complex machinery.
The type of lasers for processing the materials determines the diversity of training requirements for laser cutting technology. Thus, world buyer companies should expect a holistic training package that includes the operations of the equipment, safety protocols, and maintenance practices. Development of skillful personnel through customized training can increase the efficiency and reduce risks associated with their improper usage. This is why proper training strategizing is critical to any organization that wants to integrate laser cutting within its manufacturing processes.
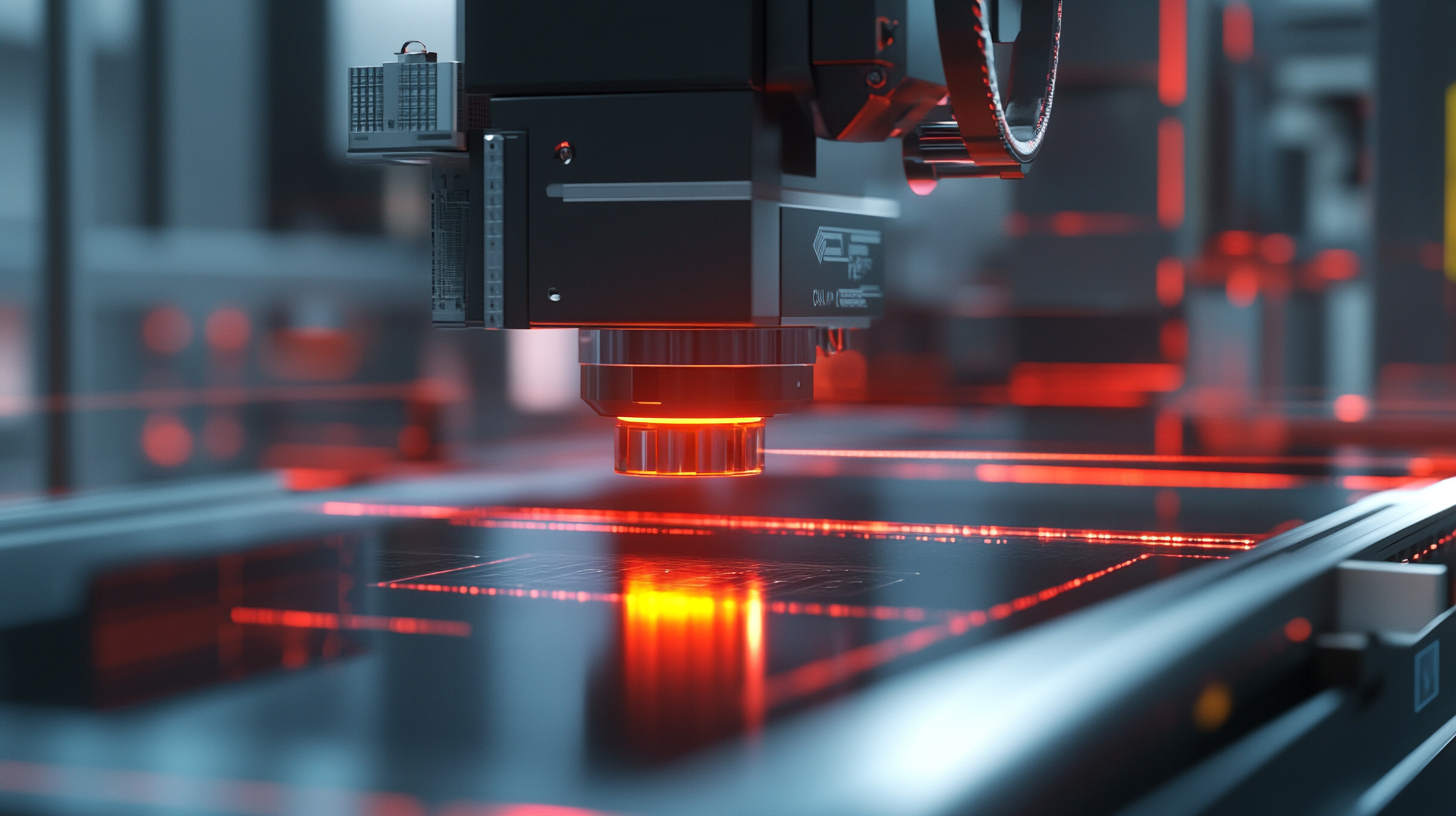
Addressing Supply Chain Challenges in Acquiring Laser Cutting Equipment
The supply chain dynamics are intricately complex; this is one of the greatest hurdles facing buyers, who are favouring laser cutting technology more than ever. With factories moving to places such as Vietnam, the sourcing of high-quality laser cutting equipment has gained prominence. Buyers are forced to work with new supply chains while adhering to the reliability and accuracy standards demanded by laser cutting applications.
The relocation of factories into Vietnam creates opportunities and threats for Chinese exports. The greater the shifts, the more demand increases for laser cutting technology; suppliers remain limited locally, and lead times have increased. Global buyers now must do more planning: identify trustworthy manufacturers and forge solid partnerships to resist the pressures of change in international trade.
Next, however, the performance characteristics of the technologies are essential. Buyers should seek suppliers that provide not only good-quality machinery but also good support from start to finish with training. This should limit production interruptions and increase efficiency of the manufacturing processes. The better positioned those who meet these supply chain challenges, as the laser cutting technology market expands, will be for a good competitive standing.
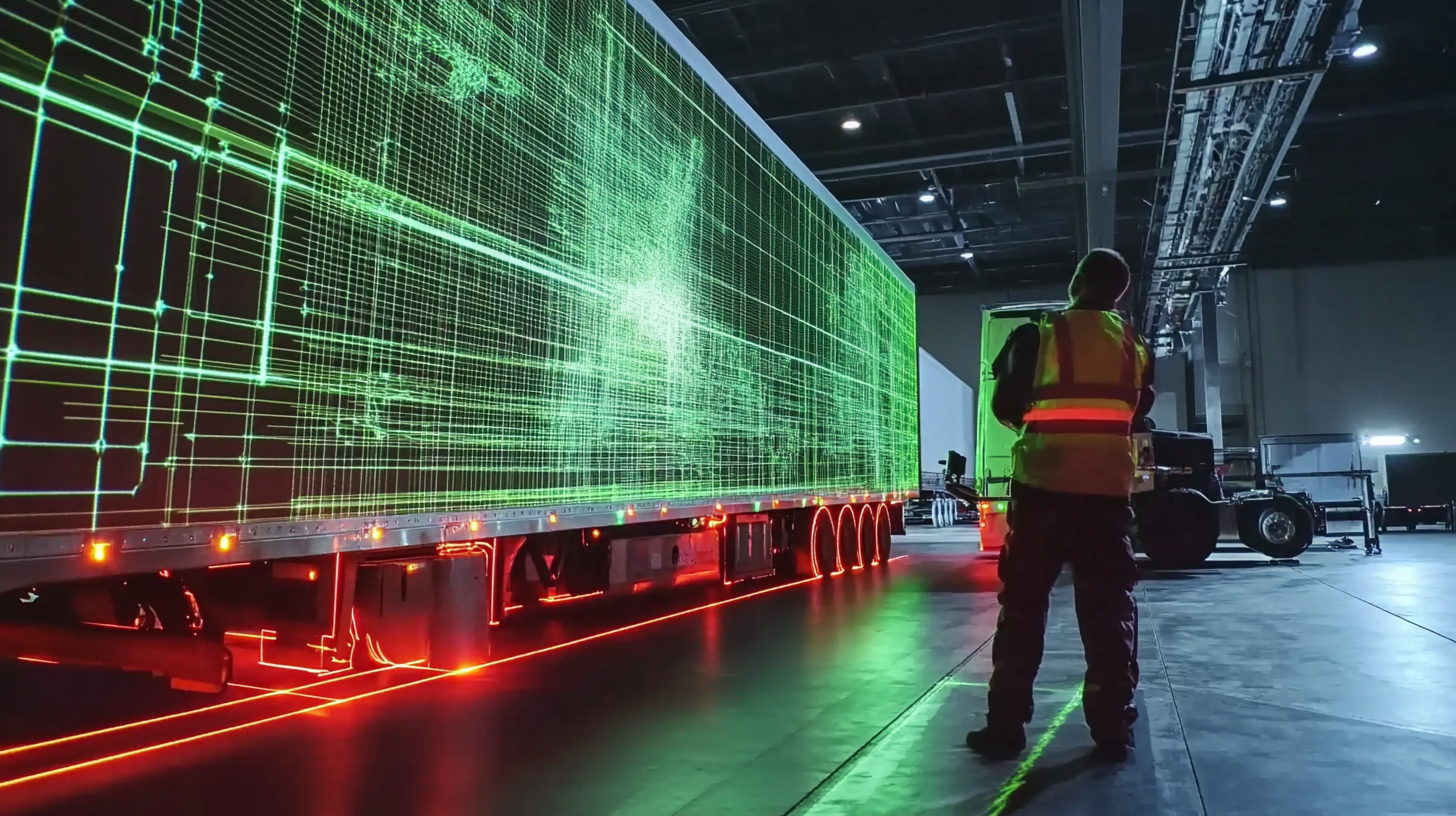
The Impact of Maintenance and Downtime on Laser Cutting Operations
Laser cutting technology was adopted in different regions of the world, taking various manufacturing processes to another level. However, one essential concern that the overseas buyers will raise is maintenance and its relatively high downtime effect to their operations. The laser cutting market is propelling towards a huge figure towards USD 6.09 billion by the year 2025, according to MarketsandMarkets, with the gradual empowerment of this technology; however, there is always a scope of unscheduled maintenance that is often seen to bring huge operational loss.
Maintenance is the factor that usually speaks for the better efficiency of such machines. Routine maintenance keeps laser cutting machines in perfect working order since lack of maintenance can give rise to poor cuts, increased waste, and high production costs. According to the research data of the Association for Manufacturing Technology, the average value of an hour owing to unplanned downtime is about 250,000 dollars that have a great impact on the efficiency of maintenance practice.
In addition, learning to operate with laser-cut technology generally aggravates the downtime. New users face real difficulties in troubleshooting and maintaining these complex systems, which results in an empty machine for longer hours. According to the International Society of Automation, organizations must have proper training and support for their employees to decrease equipment downtime. By this means of strategic maintenance planning and staff education, global buyers can be able to reduce the adverse impacts of downtime and achieve better performance in their laser cutting operations.
Exploring Industry Regulations and Compliance Issues for Laser Cutting Implementation
Challenges abound with laser-cutting technology for worldwide buyers, especially concerning navigation through industry regulations and compliance. With laser cutting becoming more common in many manufacturing areas, firms looking to employ this technology for operations must understand the regulatory landscape. Varied country standards and practices make it quite difficult for international buyers to know what safety requirements should be observed for laser-cutting equipment used and maintained.
One major area of compliance is safety and environmental regulations. Many countries have strict regulations that safeguard the operator and minimize the impact on the environment. Compliance can mean adhering to local laws and applicable international standards that dictate cross-border operations. Buyers, therefore, must commit time and resources to familiarizing themselves with these requirements, which can vary greatly from region to region. Noncompliance could lead to penalties, delays in going operational, or a prohibition on the use of the technology altogether.
In addition, regulations affect supply chains. For example, it may be equally hard to source equipment and materials compliant with specific standards for global suppliers who may not be aware of the regulations in a buyer's marketplace. Therefore, it is vital that organizations build alliances with reputable vendors that possess a strong grasp of local and international compliance matters. This foresighted approach safeguards upfront compliance while supporting a solid, sustainable application of laser-cutting technology throughout their operations.