Discovering Exceptional Suppliers for Cnc Machine Manufacturing
In the ever-evolving world of manufacturing, finding exceptional suppliers for CNC machine production is crucial for businesses striving to maintain a competitive edge. With the increasing demand for precision and efficiency, the importance of choosing the right partner in the CNC machine industry cannot be overstated. Companies must not only focus on the quality of the machines but also consider the reliability and reputation of suppliers to ensure seamless operations and superior end products.
As businesses seek to optimize their production processes, discovering suppliers that excel in CNC machine manufacturing can lead to significant advancements in both capability and innovation. From state-of-the-art technology to skilled craftsmanship, the right supplier can provide invaluable resources and expertise. This blog aims to guide manufacturers through the essential steps in identifying exceptional CNC machine suppliers, focusing on key criteria such as quality assurance, technological advancements, and customer service. By making informed decisions, businesses can enhance their manufacturing processes and drive growth in today's competitive landscape.
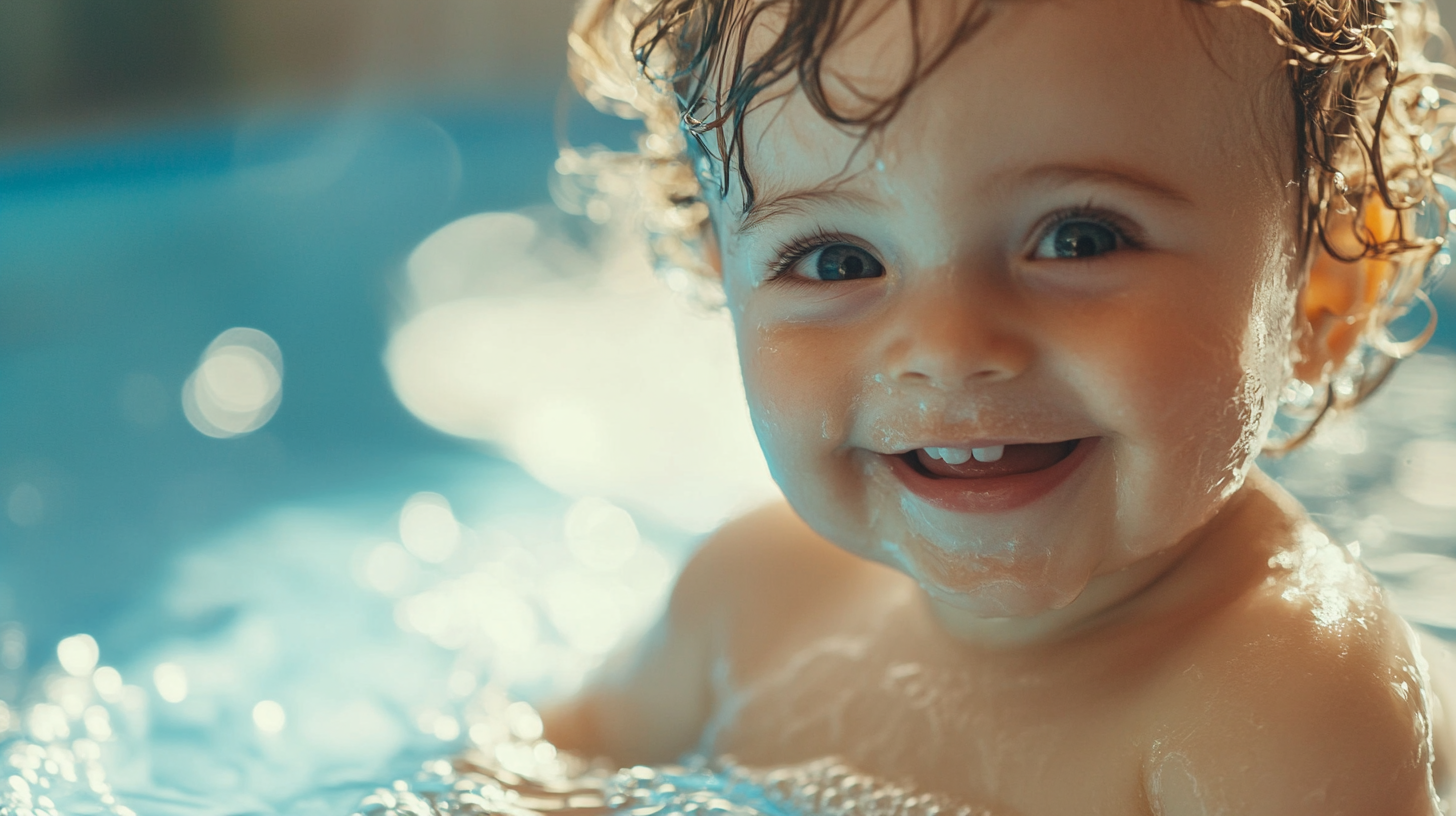
Understanding the Importance of Quality Suppliers in CNC Machining
In the realm of CNC machining, the choice of suppliers can significantly influence the quality and efficiency of the manufacturing process. According to a report by Technavio, the global CNC machine market is expected to grow by over $5 billion from 2021 to 2025, highlighting the escalating demand for precision engineering. This surge implies that manufacturers must strategically select exceptional suppliers who not only provide high-quality machines but also offer reliable support and expertise in the CNC field.
Quality suppliers contribute to reduced production downtime by ensuring that CNC machines are well-maintained and upgraded to meet industry standards. A study by Deloitte indicates that organizations that prioritize supplier quality experience up to 20% lower operational costs and 30% enhanced production efficiency. Therefore, understanding the importance of working with top-tier suppliers can foster robust relationships that lead to innovative solutions and improved manufacturing capabilities.
Furthermore, exceptional suppliers often provide access to advanced technologies and materials, which are crucial for meeting specific production requirements. Market analysts from Frost & Sullivan emphasize that embracing advanced CNC machining technologies can enhance product capabilities and open new avenues for businesses. As manufacturers navigate a rapidly changing industry landscape, partnering with quality suppliers becomes vital for sustainable growth and competitive advantage.
Key Criteria for Selecting Exceptional CNC Machine Suppliers
When it comes to selecting exceptional suppliers for CNC machine manufacturing, several key criteria must be taken into account to ensure optimal performance and quality. According to a recent report by MarketsandMarkets, the global CNC machine market is projected to reach $117.38 billion by 2025, emphasizing the rising demand for precision manufacturing. This growth underscores the importance of choosing suppliers that can provide cutting-edge technology and reliable service, which are critical in a competitive landscape.
First and foremost, the technological capabilities of a CNC supplier should be a primary consideration. Suppliers must offer advanced machinery that incorporates the latest innovations in automation and control systems. A study published by Deloitte indicates that manufacturers using advanced CNC technologies report efficiency improvements of up to 30%. This efficiency can significantly affect production timelines and cost-effectiveness, making it essential for businesses to partner with suppliers who continuously upgrade their equipment and methodologies.
Another critical criterion is the supplier's experience and reputation within the industry. A reliable supplier should have a proven record of delivering high-quality machines and services, as evidenced by client testimonials and case studies. According to the National Tooling and Machining Association, nearly 70% of manufacturers consider a supplier's background and track record before making purchasing decisions. This statistic highlights how trustworthiness and reliability are pivotal for ensuring a fruitful long-term partnership in CNC machine manufacturing.
Lastly, after-sales support and customer service play an essential role in supplier selection. Research by IndustryWeek emphasizes that businesses that prioritize strong relationships with suppliers tend to experience fewer disruptions and improved problem-solving capabilities. Exceptional after-sales service, including maintenance and rapid response times to inquiries, can greatly influence overall satisfaction, reinforcing the need to evaluate potential suppliers comprehensively. By focusing on these key criteria, manufacturers can establish partnerships that drive efficiency and innovation in their CNC machining operations.
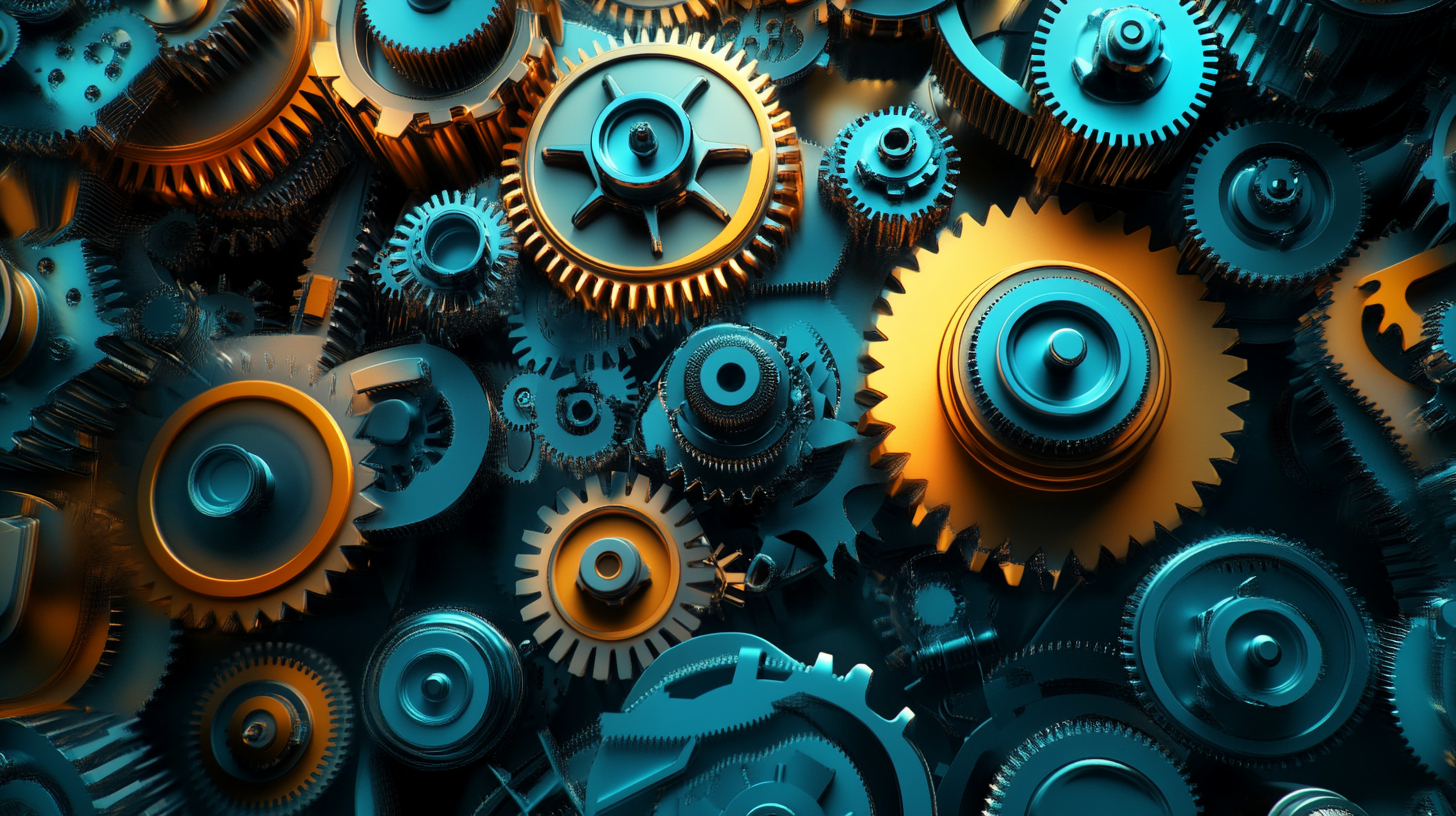
Exploring Innovative Technologies in CNC Machine Manufacturing
In the rapidly evolving world of CNC machine manufacturing, innovative technologies play a pivotal role in shaping the industry. According to a recent report by MarketsandMarkets, the global CNC machine market is projected to reach $100 billion by 2026, growing at a CAGR of 7.6% from 2021. This growth is largely driven by advancements in automation and digitization, which allow manufacturers to improve efficiency and precision in their operations.
One of the most significant technological trends is the adoption of Industry 4.0 principles, integrating smart manufacturing concepts with CNC machining processes. Implementing IoT sensors and cloud computing enables real-time monitoring and data analysis, optimizing machine performance and reducing downtime. A survey from the International Federation of Robotics (IFR) highlighted that manufacturers implementing smart technologies reported a 30% increase in productivity on average.
Another innovative development is the use of additive manufacturing techniques, which complement traditional CNC machining. By leveraging hybrid systems that combine subtractive and additive processes, companies can produce complex geometries and reduce material waste. According to a study by Wohlers Associates, the additive manufacturing industry is expected to grow to $35.6 billion by 2024, indicating a robust intersection with CNC technologies that enhances design flexibility and efficiency in production.
As the landscape of CNC machine manufacturing continues to evolve, staying abreast of these technological advancements is crucial for suppliers. Those who adapt to the latest innovations will not only enhance their competitiveness but also meet the growing demands of various industries, from aerospace to healthcare.
Building Strong Relationships with Your CNC Suppliers
In the competitive landscape of CNC machine manufacturing, building strong relationships with your suppliers is crucial for success. These partnerships can greatly influence the quality of your products and the efficiency of your operations. When you take the time to invest in these relationships, you establish a foundation of trust and loyalty that can lead to mutual growth and innovation. Engaging with your suppliers on a personal level fosters open communication, allowing for better alignment in business processes and collaborative problem-solving.
Moreover, developing these connections can lead to enhanced support for your projects. For instance, ongoing interactions can provide valuable insights into trending CNC projects and emerging technologies, enabling you to adapt your offerings to meet market demands. By understanding the capabilities and timelines of your suppliers, you can streamline production and optimize your inventory, ensuring that you meet customer expectations without unnecessary delays.
As exemplified by companies that have maintained close ties with their supply chains, the benefits of a strong relationship extend beyond immediate operational advantages. These partnerships can also spur innovation, helping you explore new product ideas and trends, such as profitable CNC projects anticipated for the coming years. Ultimately, prioritizing supplier relationships is not just a strategy for today but a foundational approach for sustainable growth in the future.
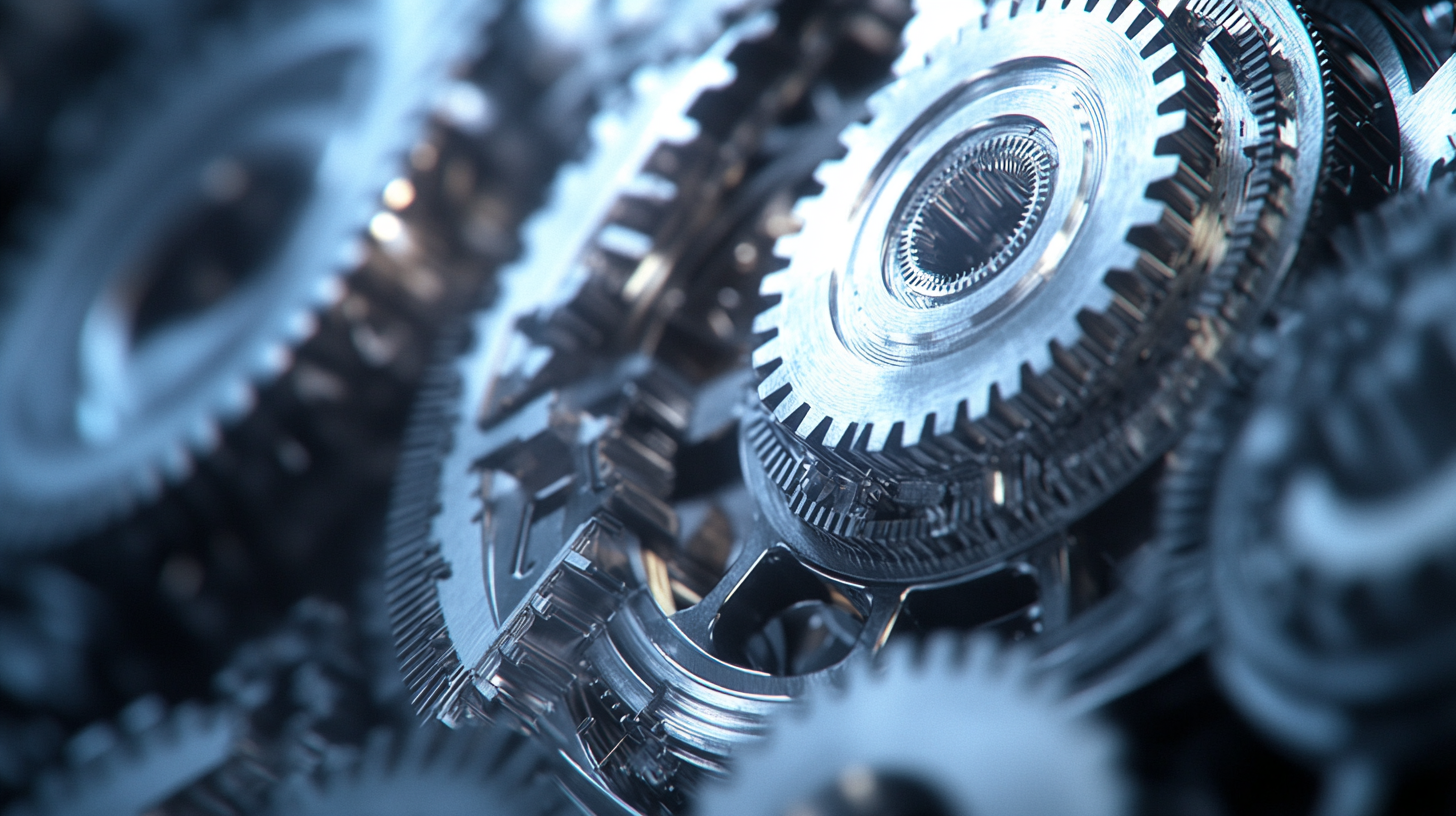
Evaluating Supplier Performance: Metrics and Best Practices
When it comes to CNC machine manufacturing, selecting the right suppliers is crucial for maintaining quality and efficiency. Evaluating supplier performance through effective metrics can significantly influence your production outcomes. First and foremost, you should consider metrics such as on-time delivery, product quality, and responsiveness. These key performance indicators (KPIs) enable manufacturers to gauge how well a supplier is meeting contractual obligations and customer expectations.
Additionally, implementing regular performance reviews can enhance supplier relationships and uncover areas for improvement. Techniques like vendor scorecards provide a structured approach to assess performance over time, enabling manufacturers to track trends and identify potential issues before they escalate. Incorporating feedback mechanisms where suppliers can respond to evaluations fosters an environment of continuous improvement and collaboration.
Another best practice is to benchmark suppliers against industry standards. This not only helps to measure performance objectively but also encourages suppliers to elevate their service levels. Engaging in open discussions about these metrics allows both parties to align on goals and expectations, resulting in a stronger partnership. By focusing on these evaluation strategies, manufacturers can discover exceptional suppliers that contribute positively to their CNC machining processes.
Supplier Performance Evaluation Metrics
Related Video
-
Unrivaled Precision Machining Solutions for Your Custom Projects#precisionmachining #fabrication
View: 6Channel: Fair Shine Industrial (HK) Co.,Limited -
Discover CNC Machine Manufacturer
View: 1Channel: LiSN Machinery -
Discover Why Naseiko is China’s Biggest CNC Tool Grinder Supplier
View: 54Channel: Naseiko