Unlocking the Future of Manufacturing with Cnc Tools 2025 Trends and Essential Buying Guide
With preparations for 2025 abound, the technology-led paradigm of manufacturing is set for revolutionary changes, especially with new advances in CNC tools. According to MarketsandMarkets, the CNC machine market globally is forecast to grow to USD 100 billion by the year 2025, growing at a CAGR of 6.8% from the base year of 2020. This growth results from the rising need for precision and efficiency in manufacturing methods and the increase in demand for customized products in different industries. CNC tools are the spearhead of this technological transformation, allowing manufacturers to not only enhance productivity but also to minimize wastage and enhance product quality.
Industry 4.0 and smart manufacturing are transforming the landscape on which businesses look at CNC tools, linking them with IoT and AI to optimize operations. A Deloitte study discovered that advanced CNC technologies have helped the company increase operational efficiency by as much as 20%. Against this backdrop, as awareness increases among manufacturers on how these tools constitute a competitive advantage, a clear understanding of the latest trends and informed decisions in their choice will become imperative. This blog discusses the key trends affecting the future of CNC tools, with buying advice that helps manufacturers make their way through the turbulent waters of these ever-evolving tools.
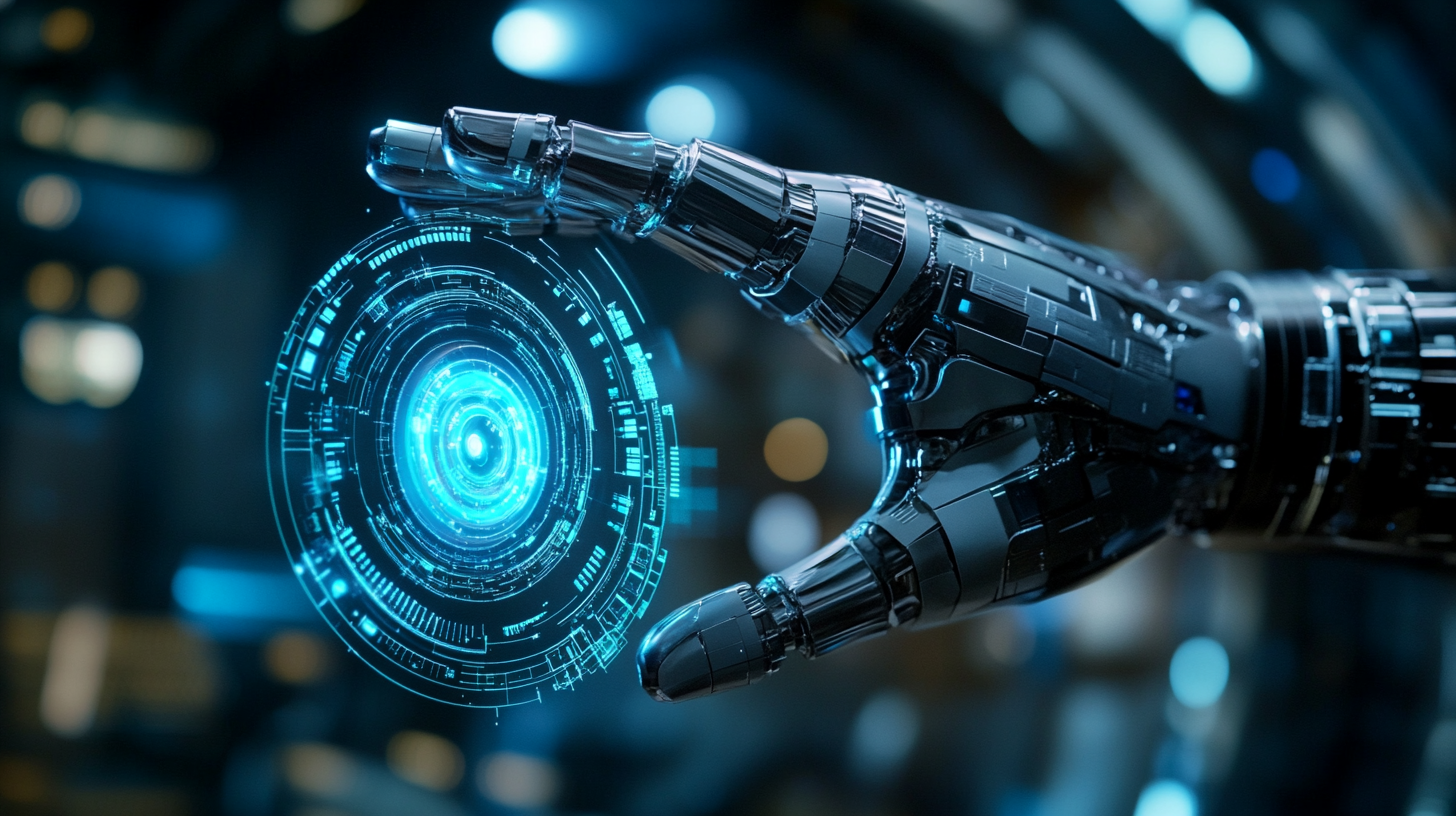
The Evolution of CNC Tools: What to Expect in 2025
The cutting tools industry, by its very nature, is characterized by rapid change due to new technologies and evolving market demands. The latest report by MarketsandMarkets states that the global CNC machine market is expected to reach $100 billion by 2025 at a CAGR of 7.5% for the period 2020 to 2025. Growth is mainly due to the increasing levels of automation in manufacturing, thereby improving precision and efficiency. Somewhere in 2025, we might witness CNC tools embedded with AI and machine learning for even further optimization of cutting processes and waste reduction. McKinsey's study mentions that these AI-assisted CNC machines can increase productivity by about 20%, which will again help manufacturers stay in contention in a highly globalized market. Innovative processes like adaptive machining will allow these tools to learn from their past operations, bringing about continuous improvements and lowering their operating costs. There is also a growing demand for sustainable manufacturing systems, resulting in manufacturers looking for eco-friendly CNC machines. According to a Deloitte survey, 60% of manufacturers intend to invest in sustainability technologies by 2025, including CNC machines that conserve energy and reduce material waste to cut carbon footprints. The trend points toward a paradigm shift toward green practice adoption for the manufacturing community. Therefore, having the right choice of CNC tools may have an economic significance moving forward.
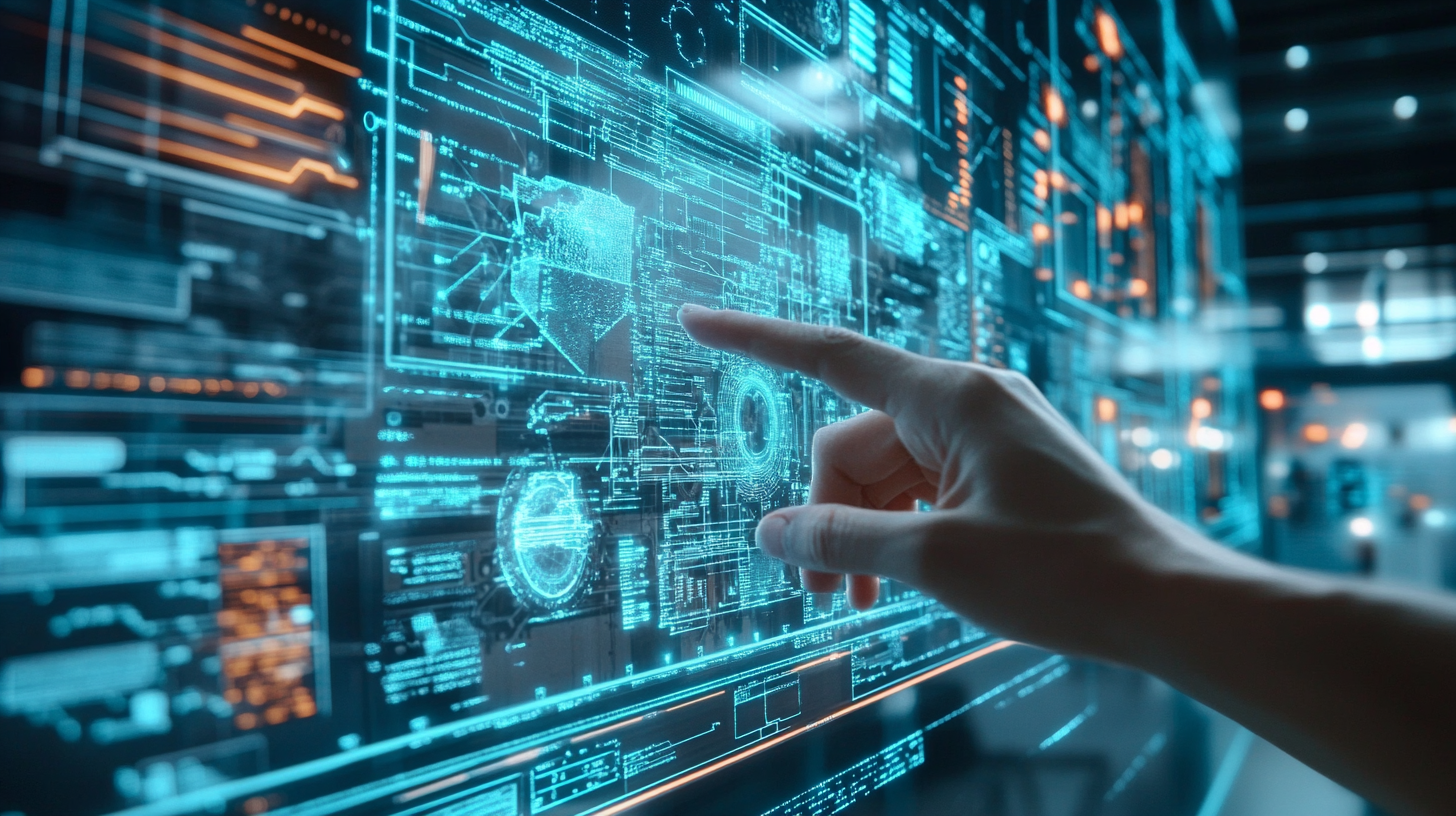
Key Trends Shaping the Future of CNC Manufacturing
CNC manufacturing is currently undergoing rapid advancement due to the evolution of technology and the changing market demand. Major trends shaping the future will include automation and artificial intelligence integration into manufacturing processes. The global CNC machining industry size is expected to hit $100 billion by 2025, growing at a CAGR of 7.1%, as stated in a report by Research and Markets. This demand stems from the need for precision and efficiency since companies are trying to improve their production capabilities.
Another trend is the advancement in Industry 4.0 that puts emphasis on smart connected machines and data-centric business decisions. According to a report by McKinsey, companies using IoT-enabled CNC machines saw an increase in productivity of up to 30%. This transition allowed manufacturers to optimize their operations, running their machines more efficiently and minimizing downtimes in the workflow. The collection of real-time data, in turn, allows for collective and predictive maintenance to reduce unforeseen failures and operational interruptions.
Sustainability is also on the agenda now for CNC manufacturing. According to the Global CNC Machine Tools Market report, almost 60% of manufacturers are investing in green technologies and processes. Sustainable practice not only conforms to regulations but alsocomes with consideration for growing consumer preference for green products. These trends are going to shape the future of CNC manufacturing and help the companies which adapt to gain a competitive advantage in the market.
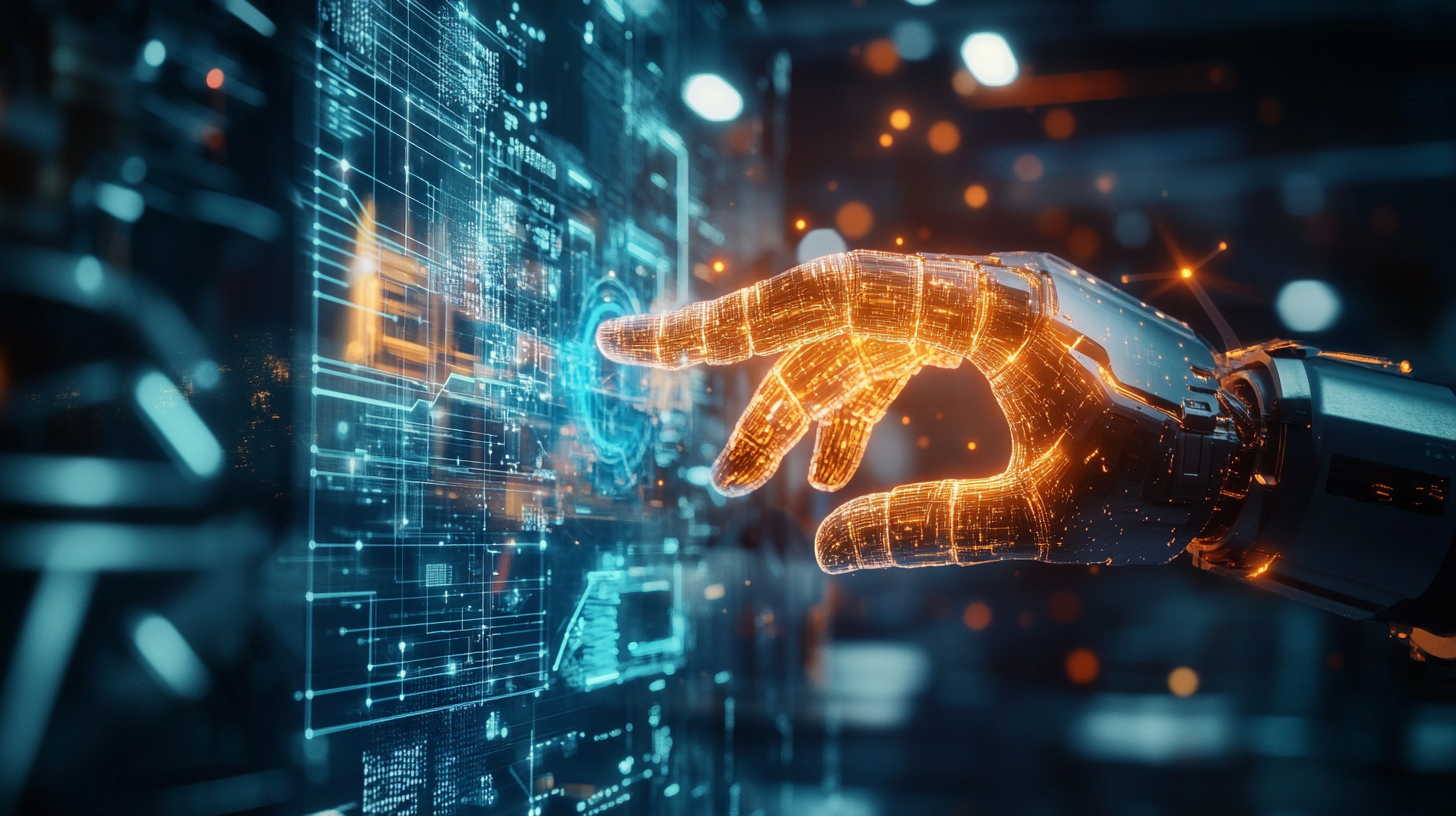
Essential Features to Look for When Buying CNC Tools
Understanding the essential features of CNC tools for manufacturing processes is integral in making good investment decisions. The rapid changes in technology expected in 2025 make it imperative for manufacturers to look for performance features such as efficiency, precision, and ease of use. One such feature is automation. Automated tools bring down labor costs, reduce human intervention, and thus, allow production at rapid rates with little compromise on quality.
The machine's compatibility with various materials is another important aspect to consider. As manufacturing requirements become more varied, CNC tools should have the appropriate versatility to accommodate different substrates including metals and plastics. A tool with more material applications, therefore, will allow that investment to remain relevant as market requirements change. An intuitive user interface is also a crucial consideration since an easy-to-operate control system would reduce the operator's learning curve to almost zero, thus aiding in quick integration into existing workflows.
Last but not least, ensure that there exist strong support and training programs offered by manufacturers. The evolution of technology tends to increase the complexities of CNC tools, making support anytime an asset. Thus, if your chosen tools come with great tech assistance and training options, it will help ensure that your operations run with maximum efficiency and that your investment has a long life. When focused on these critical aspects, manufacturers can build a path to success in the mega environment of CNC machining to come.
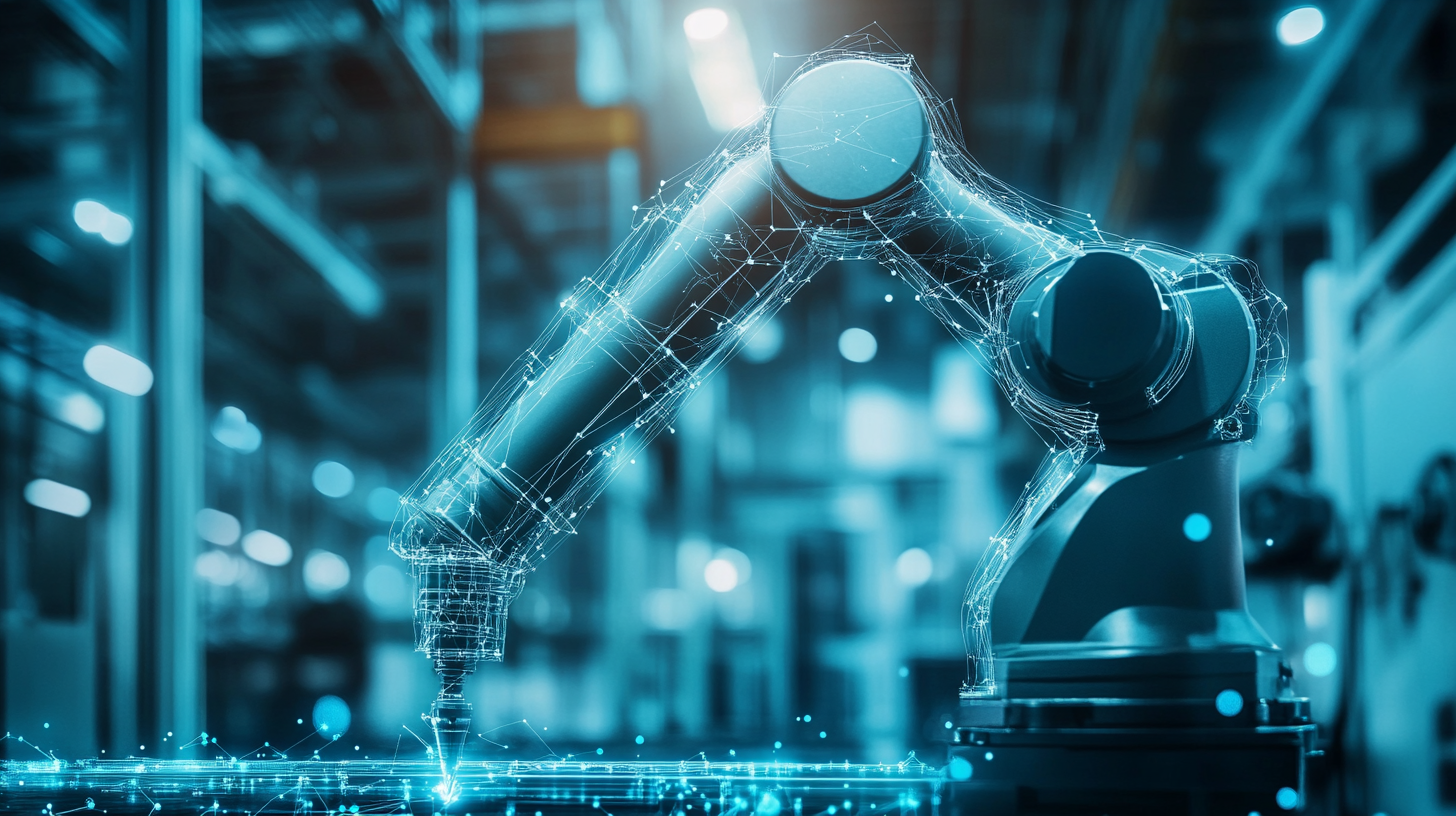
Cost vs Quality: Making Smart Purchasing Decisions
Since the manufacturing industry keeps changing quickly, weighing the cost against the quality should be very prudent regarding CNC tools acquisition. Most businesses reach a point where they have to make decisions on their production capability enhancement. Would companies go cheaper but sacrifice performance or use expensive and quality tools with precision and reliability? The factory floor is full of such dilemmas for engineers as they face the growing concern among manufacturers around the 2025 predictions.
CNC tool selection is rather complicated. Genuinely, excellent tools tend to be very precise as well as long-lived, thus costing less in a time perspective due to infrequent replacement and maintenance. However, cost-efficient CNC machines could seem fully enticing and then lead to their users incurring high operational costs due to increased abrasiveness and below-standard performance. Hence, while designing their purchasing decisions, manufacturers should concentrate on a long-run perspective that correlates with their production goals and expected output.
Besides, the evaluation of the supplier's repute and the warranty given might uncover the hidden costs of tool acquisition. Usually, a well-known supplier provides full support, quality guarantees, and hints on adequately using their tools, thus greatly enhancing one's returns on investment. Intelligent purchases therefore depend on the total worth provided by CNC tools in a lifetime cross your manufacturing processes, rather than upfront cost.
Integrating Smart Technology into CNC Operations for Enhanced Efficiency
Smart technology has come with its own CNC operations that are redefining the manufacturing activities within a sphere of efficiency and productivity. Recent reports have revealed how the projections for the global CNC machine market would grow significantly over recent years, mainly due to new advanced controllers and industrial automation. In particular, the rise of Industry 4.0 is changing modes of classical manufacturing because businesses are leveraging and embracing digitalization and smart technologies to streamline their operations. Furthermore, the CNC market is estimated to reach an approximate size of the market worth $100 billion by the year 2025, which explains the very essence of technological advancements in spurring industrial growth.
For example, the advent of the latest five-axis CNC machine fitted with an advanced controller being manufactured locally typifies this trend toward achieving increased efficiency, boasting speeds of up to 35% faster than those on conventional machines. Such approaches showcase the capability of implementing smart technology in CNC operations and also give reference points to manufacturers looking to upgrade their capabilities. Instead of relying on humans to perform these processes, manufacturers could also utilize collaborative robotics with loading and unloading functions to prevent fatigue from occurring due to repetitive tasks and increase machine production rates. In this way, automation illustrates complementing CNC machinery toward achieving operational excellence.
Further, sector-based applications such as automotive and precision machineries are slowly incorporating such benefits. The phenomenal increase in demand for precision components has made the relevance of CNC tools piercing deep within metal cutting and forming apparent. Indeed, smart technology is set to change the course of operational efficiencies across these industries. As such, it is increasingly becoming vital for manufacturers to keep pace with such trends as they are transformational.