The Evolution of Cnc Drilling Machines in Global Manufacturing Trends
From modern global manufacturing, the CNC drilling machine makes all the difference in improving efficiency and accuracy in production. To keep pace with ever-increasing demands for quality and speed, industries have turned basic manual tools into today's CNC drilling machines, highly sophisticated automated systems. This evolution signifies not only advances in technology but also the evolving face of manufacturing processes, with a focus on greater efficiency and reduced human error.
Over time, improvements to CNC drilling machines have included very sophisticated features such as high-tech software, real-time monitoring, and advanced capabilities that handle multiple kinds of materials and applications. This has made the difference to the way manufacturers now do things, allowing even more sophisticated designs and shorter production cycles. Where one opens the portals into what current trends are shaping in the arena of global manufacturing, it becomes very obvious that the CNC drilling machine is not just a tool but the cornerstone of modern manufacturing strategy, innovating and creating advantage across sectors transfixed on competing with one another.
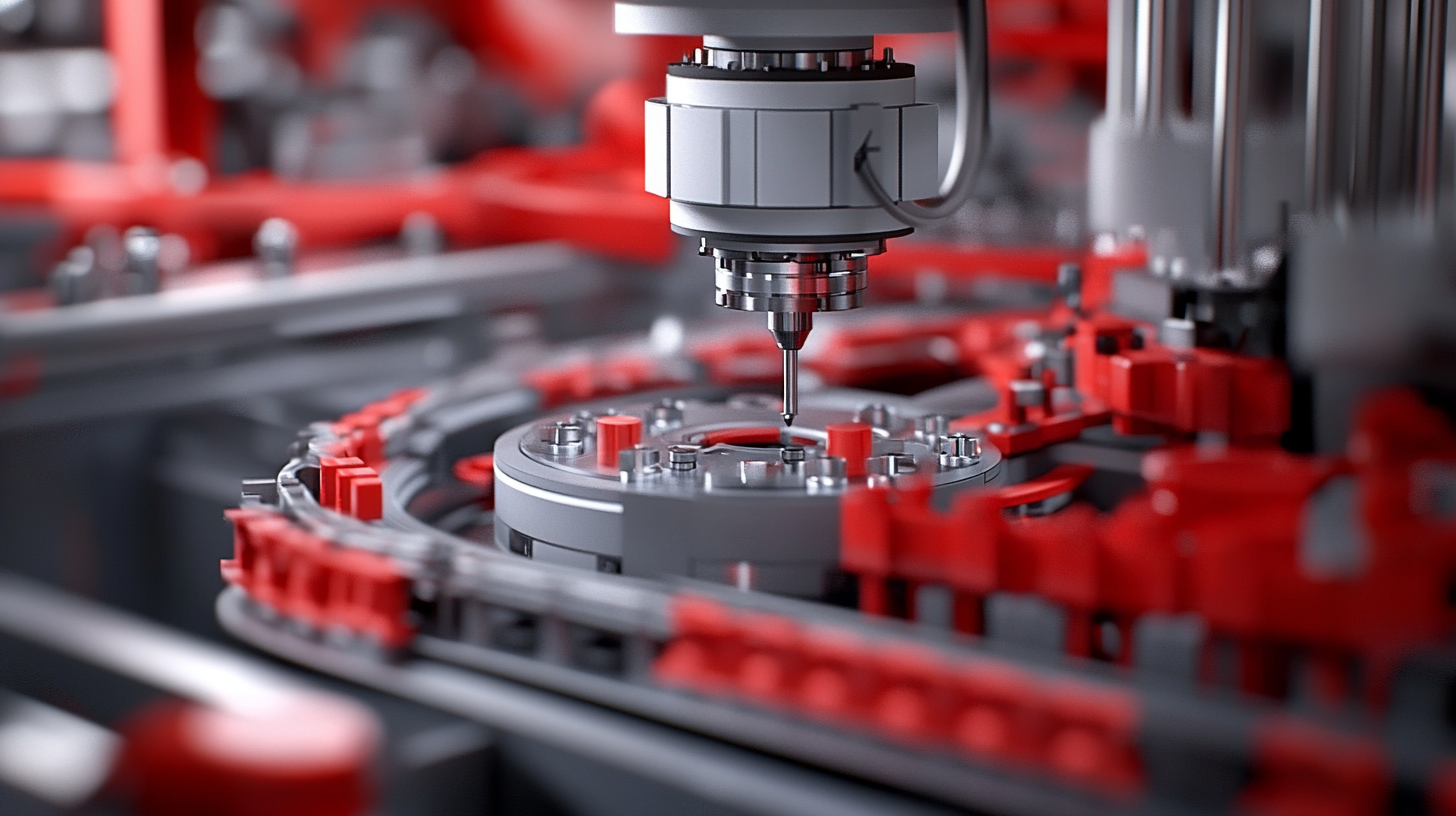
Historical Overview of CNC Drilling Machines in Manufacturing
CNC drilling machines have a history that is as interesting as it is reflective of global manufacturing trends. Traditional drilling machines were based totally on personnel operations, totally mechanical and the very boring groundworks of industry offering only very simple utility for the automotive and for general machinery. They have not been very much revised and enhanced since then. However, as the demand for precision and efficiency increased, manufacturers sought technologically advanced machines. When Computer Numerical Control (CNC) technology was introduced, it would bring a revolution to drilling operations. The automated operations of CNC machines could drill with very high precision, and it reduced human errors and increased productivity. This has significantly contributed to the operational efficiency parameter and expanded the traditional area, making it one of the basic techniques in precision engineering and transportation manufacturing. As the CNC technology further developed, several highly intricate features matured as new upgrades such as multi-axis drilling capability and software integration for better control and design. Rising demands from many geographical areas absolutely multiplied the market for machine tools especially made for CNC drilling machines. Today, such has become CNC machines for industries wishing to remain very competitive, often investing massive amounts toward keeping up with advances in technological advancements in the face of further competition in terms of market needs.
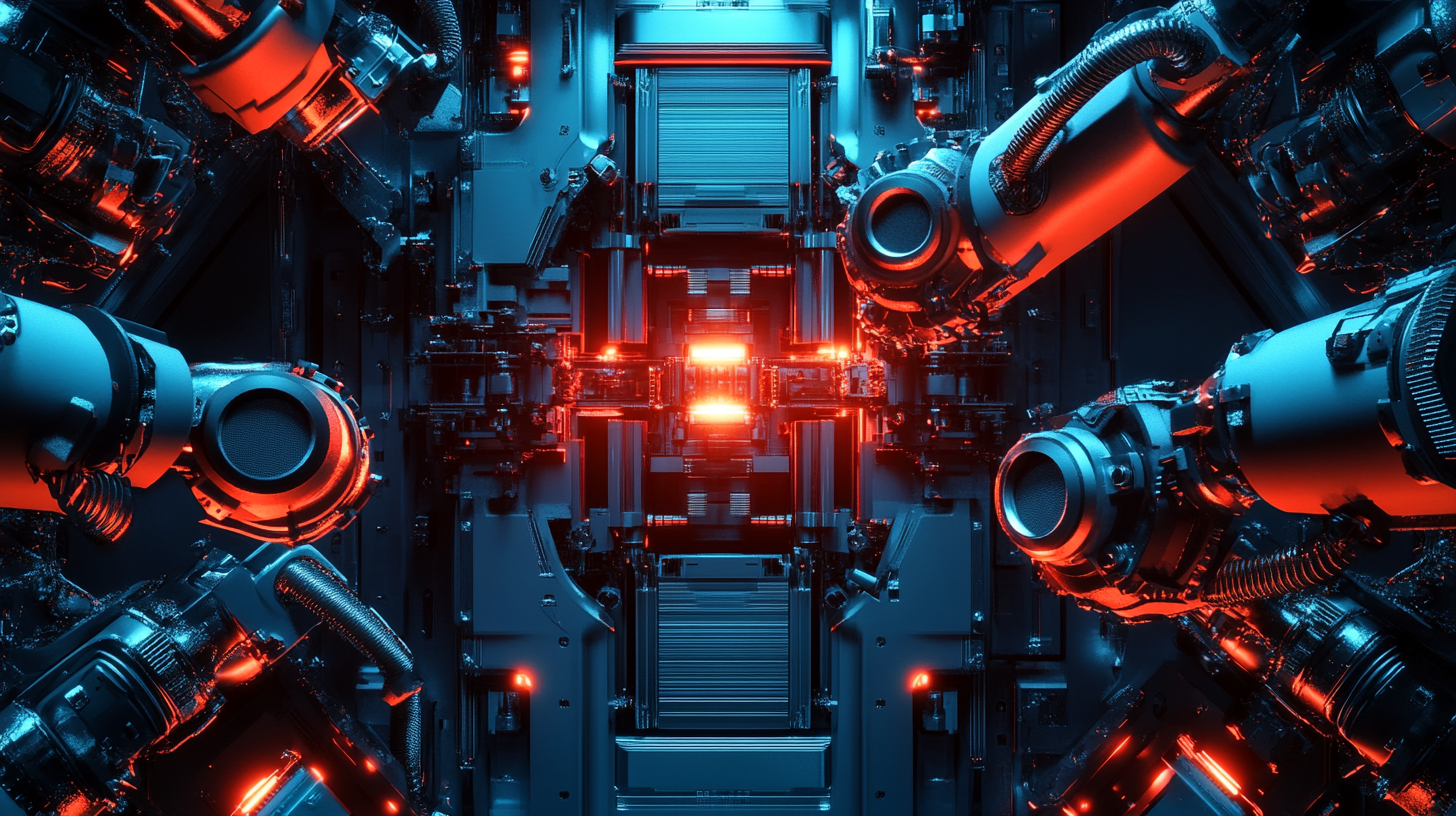
Key Technological Advancements Shaping CNC Drilling Machine Capabilities
CNC drilling machine improvements have systematically altered manufacturing trends across the globe. Therefore, nowadays, industries keep precision and efficiency in focus. With automation, real-time monitoring, and smart materials, these machines have become far more modern in their functionality. Present-day CNC drilling machines not only cut but also involve high-end software to support intelligent programming and flexible operation. This paradigm shift has made production lean, enabling manufacturers to satisfy evolving demands from different industries, such as automotive as well as precision engineering.
The existence of the Internet of Things (IoT) further facilitates an adaptive approach to manufacturing. CNC drilling machines are networked and are capable of real-time data analytics and predictive maintenance. This advancement not only boosts operational efficiency but also reduces machine downtime, thereby affecting the bottom line of manufacturing companies. With the input from Internet of Things-enabled technologies, machine performance can be monitored remotely and the system enabled for a rapid response to adjust production lines according to changes in market demand.
Further, the market for CNC drilling machines continues to expand, mainly due to growing automation and advanced technology focus. As manufacturers invest in sophisticated machinery, sustainability and energy efficiency will likely come into the limelight, critical topics in modern-day industrialism. Thus, these advancing technologies make the manufacturing processes easier to execute, yet in conjunction with the current global drive for environmentally sound practices, signify a total shift in its own right in the CNC drilling machine industry.
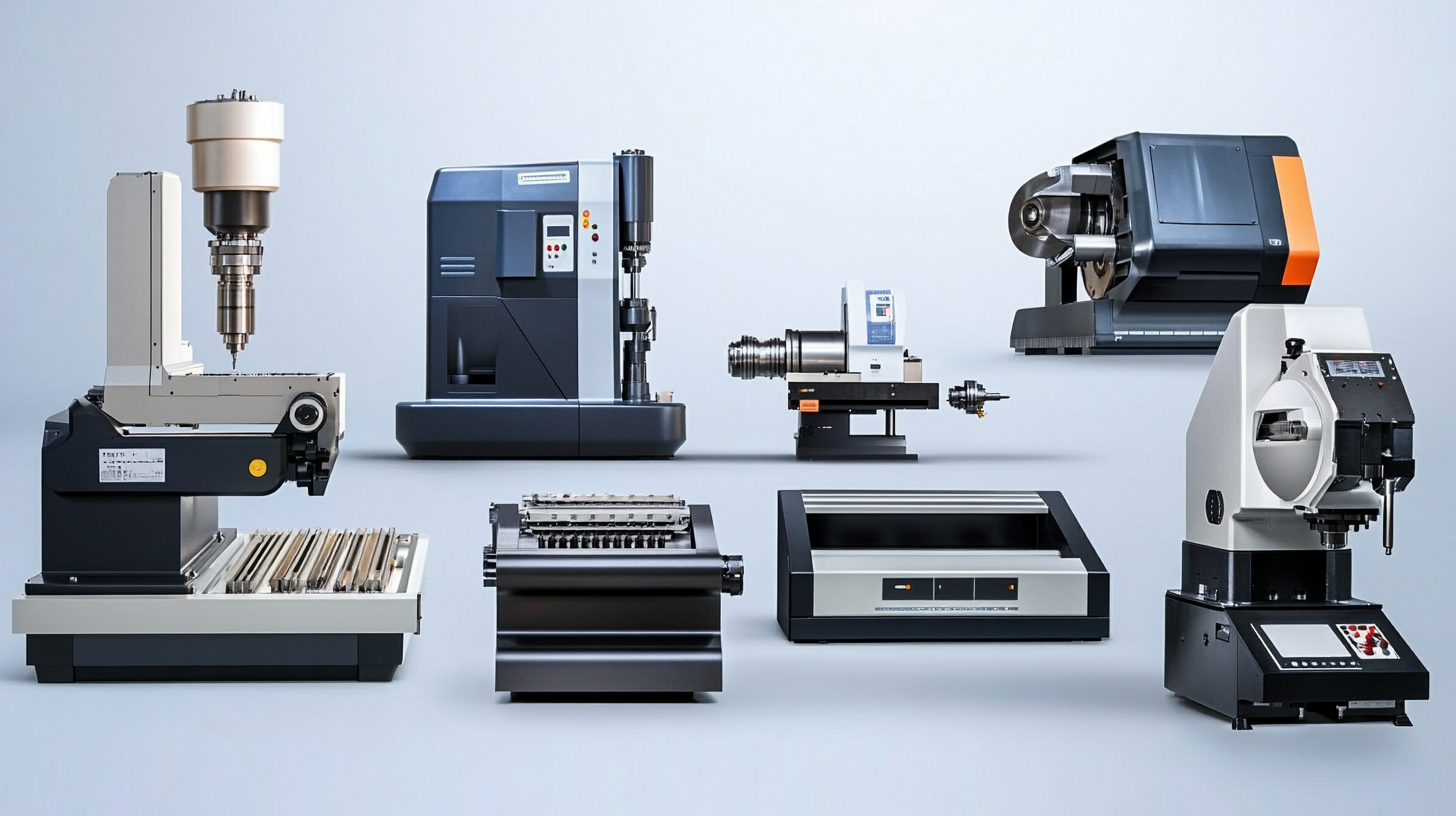
The Role of CNC Drilling Machines in Modern Industry Applications
CNC drilling machines have become increasingly pivotal in modern industrial applications, emphasizing an important role in enhancing precision and efficiency in various manufacturing industries. As industries develop, the need for reliable and advanced machining tools becomes necessary to keep up with increasing demands for quality and speed. Therefore, these machines have modernized old drilling processes and allowed manufacturers to design parts that require complex designs with high accuracy and consistency.
On the other hand, recent advancements, such as establishing certification centers for CNC milling in Hualien, evidence the industry's resolve in closing the gap between academia and practical application. This initiative aims at producing skilled technicians who will be able to control sophisticated CNC equipment, which will enable industries to keep in step with world manufacturing trends. Thus, much effort by educational institutions in creating the CNC technology base will help prepare the next crop of engineers and technicians.
Besides, the versatility of CNC drilling machines has found numerous applications in different fields such as aerospace and automotive and electronics. Automation of the drilling process not only minimizes human error but also substantially reduces production times-which gives firms the upper hand in this increasingly competitive market. The evolution of CNC drilling machines, as well as their current and future applications in modern industries, will continue to drive innovation as manufacturers fully embrace these advanced technologies.
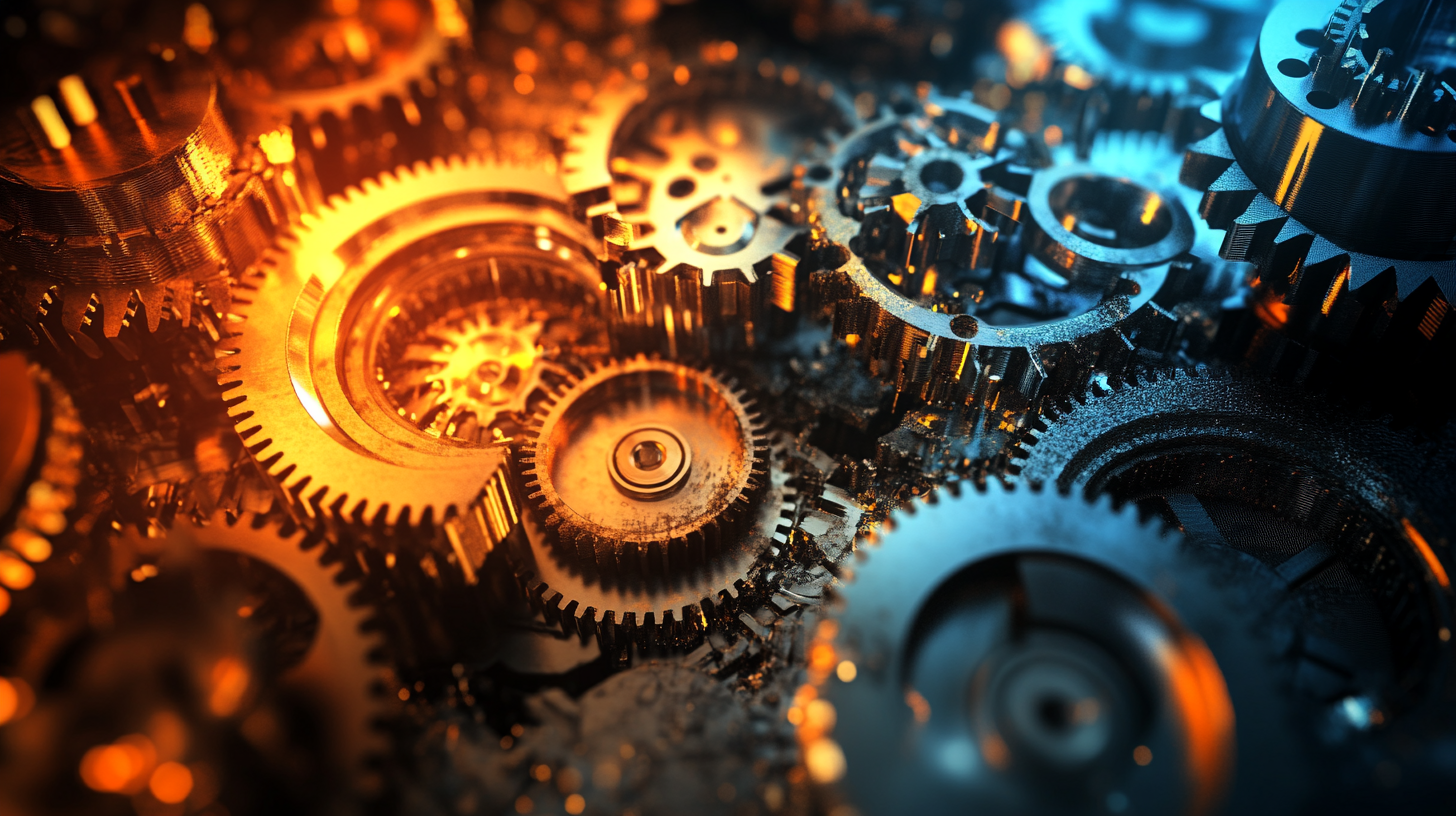
Global Manufacturing Trends Influencing CNC Drilling Innovations
Innovations in the CNC drilling machine industry have given rise to trends that are being significantly influenced by global manufacturing realities. One major driving force is the demand for precision engineering in several areas such as aerospace and automotive. The global CNC machine market will total around $100 billion by 2026, as seen in the report released by MarketsandMarkets, which shows a gradual shift toward advanced automation and efficiency in takeovers, hence pressuring manufacturers to integrate sophisticated CNC drilling technologies that add an accuracy level and decrease operational expenditure.
The trend mergers drive this facet while taking advantage of the new paradigm in Industry 4.0. The introduction of the IoT along with other smart manufacturing software is a way of collating and analyzing data at real time, which would allow decision making to become a more informed practice. According to McKinsey research, it is said that organizations using IoT solutions improve operational efficiency by 20-30%. As such, the investments for CNC drilling machines are focused more on smart-dependent technologies that perform the automatic optimization of drilling parameters, minimizing wastage, and improving the product quality.
Sustainability is yet another emerging force which is driving evolution in CNC drilling machines. Regulatory pressure is mounting, as is a call from consumers for green practice, and manufacturers have started looking at ways to form a green supply chain that would reduce energy consumption and material waste in processes. As noted by the International Energy Agency, improved machining technologies could cut manufacturing energy use by more than 30%. Sustained manufacturing can not only help a company meet compliance standards but also bolster its competitiveness in the market further driving the call for innovation in CNC drilling solutions.
Future Prospects and Emerging Technologies in CNC Drilling Machines
The CNC drilling machine has gone through a lot of transformations over the ages in their adaptation into the changing world of manufacturing. The CNC drilling machines of the future will be defined largely by some emerging technologies as industries move towards more and more automation and precision. One of the major advancements, however, is that of artificial intelligence (AI) and machine learning. These disciplines enable CNC machines to learn from previous performances, optimize drilling parameters in the real-time as well as predict tool wearing, thereby producing and minimizing downtime.
Another important developing trend is the tenet of Industry 4.0, with its focus on interconnectedness and data sharing among machines. IoT-sensor-enabled drilling machines are able to transmit and provide deep analytical intelligence, helping manufacturers in fact make use of informed decision making and remote conduct of operations on board equipment. Obviously, such connected machines not only create efficient flow processes, but also help prevent maintenance interventions, thereby avoiding disturbances and extending equipment life.
Sustaining awareness becomes increasingly of important requirement in CNC drilling technology. The machines build energy efficiency and environmentally friendly practices in the markets. Further, advancements in materials like lighter alloys and composites keep pushing the boundaries further of what CNC drilling can do allowing the more complicated and lighter designs to be produced. The future of CNC drilling machines promises to lead towards more efficiencies and productivity-also in an environmentally friendly manner.