Exploring the Unique Features and Applications of CNC Cutting Across Industries
CNC cutting has revolutionized the manufacturing landscape across various industries, becoming an essential process for precision and efficiency. According to a report by MarketsandMarkets, the global CNC machine market is projected to reach USD 117.85 billion by 2025, with a significant portion attributed to CNC cutting applications. This technology enables manufacturers to produce intricate designs with a level of accuracy that manual cutting methods cannot achieve, thereby reducing material waste and enhancing productivity. The versatility of CNC cutting extends to diverse sectors, including aerospace, automotive, and metal fabrication, where tailored solutions are paramount.
As industries continue to seek innovative ways to optimize their operations, CNC cutting stands out for its ability to adapt to different materials, ranging from metals and plastics to wood and composites. A study from Grand View Research reveals that the demand for CNC cutting technologies is expected to grow at a compound annual growth rate (CAGR) of 6.2% from 2021 to 2028, driven by the increasing need for custom parts and components. This blog will explore the unique features and applications of CNC cutting, illustrating how it not only transforms production processes but also enhances the competitive edge of businesses across various sectors.
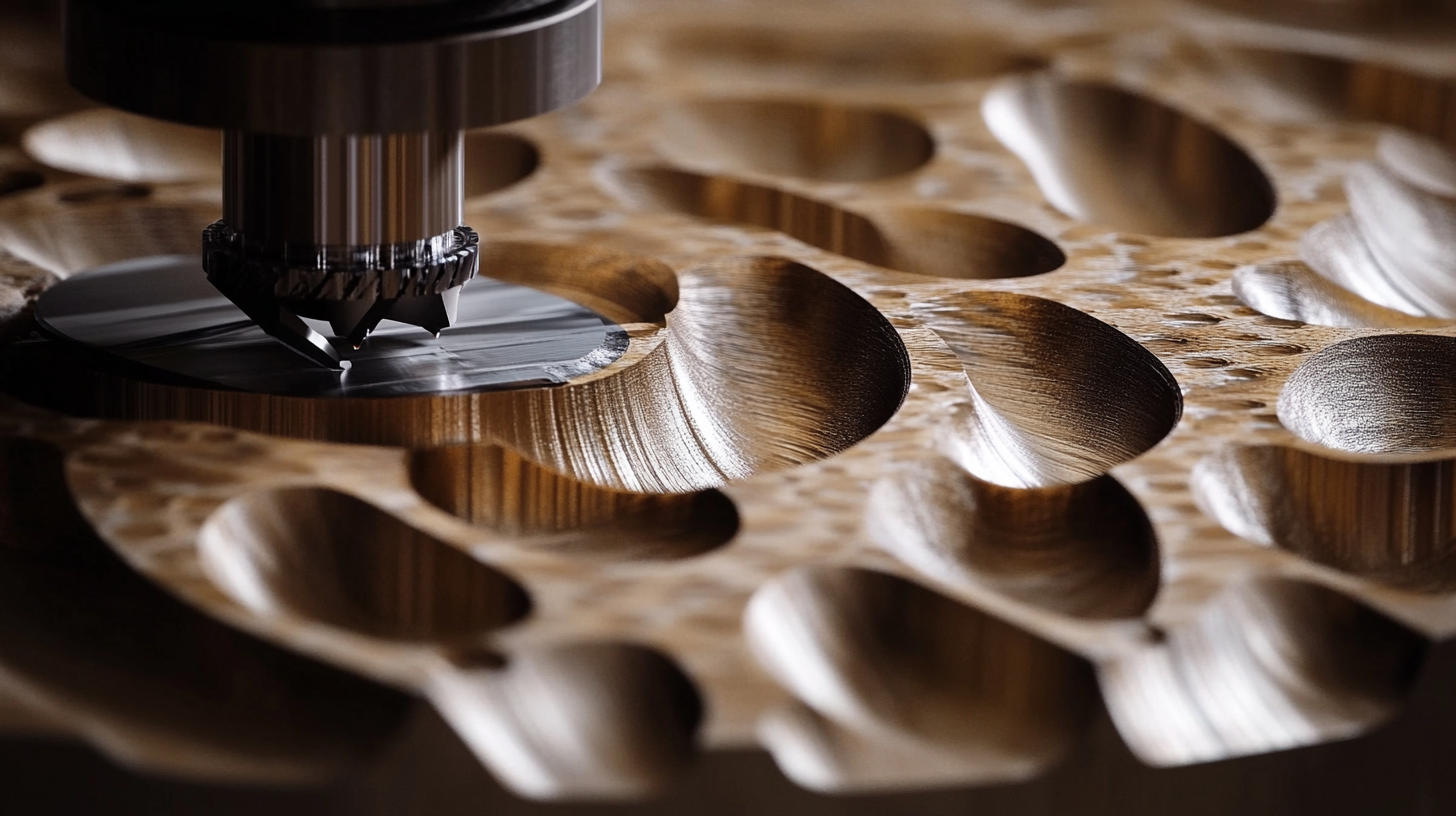
The Evolution of CNC Cutting Technology: Key Milestones and Advancements
The evolution of CNC cutting technology has significantly transformed manufacturing processes across various industries. From its inception in the mid-20th century, CNC cutting has undergone remarkable advancements, enabling precision and efficiency that were previously unattainable. Early CNC machines were limited in versatility and capabilities, primarily focusing on simpler tasks. However, developments such as multi-axis machining, improved software interfaces, and the implementation of automated systems have revolutionized the way manufacturers approach complex designs. Today, CNC cutting technology encompasses a range of applications, including metal cutting and forming, which are critical in industries such as aerospace, automotive, and woodworking. The integration of features like laser cutting and 3D printing into CNC machines, for instance, showcases the versatility and adaptability of the technology. This progress not only enhances production efficiency but also allows for greater creative freedom in design. Innovations in user-friendly interfaces have made these advanced machines accessible to a broader range of operators, fueling the growth of CNC applications in both small workshops and large-scale manufacturing environments. As we look to the future, the potential for CNC technology continues to expand with the advent of smart manufacturing. The incorporation of IoT (Internet of Things) capabilities and real-time monitoring promises to optimize machining processes further, minimize downtime, and reduce waste. This evolution paves the way for smarter, more resilient manufacturing ecosystems that can adapt to the ever-changing demands of the market, reinforcing CNC cutting's essential role in modern engineering and production.
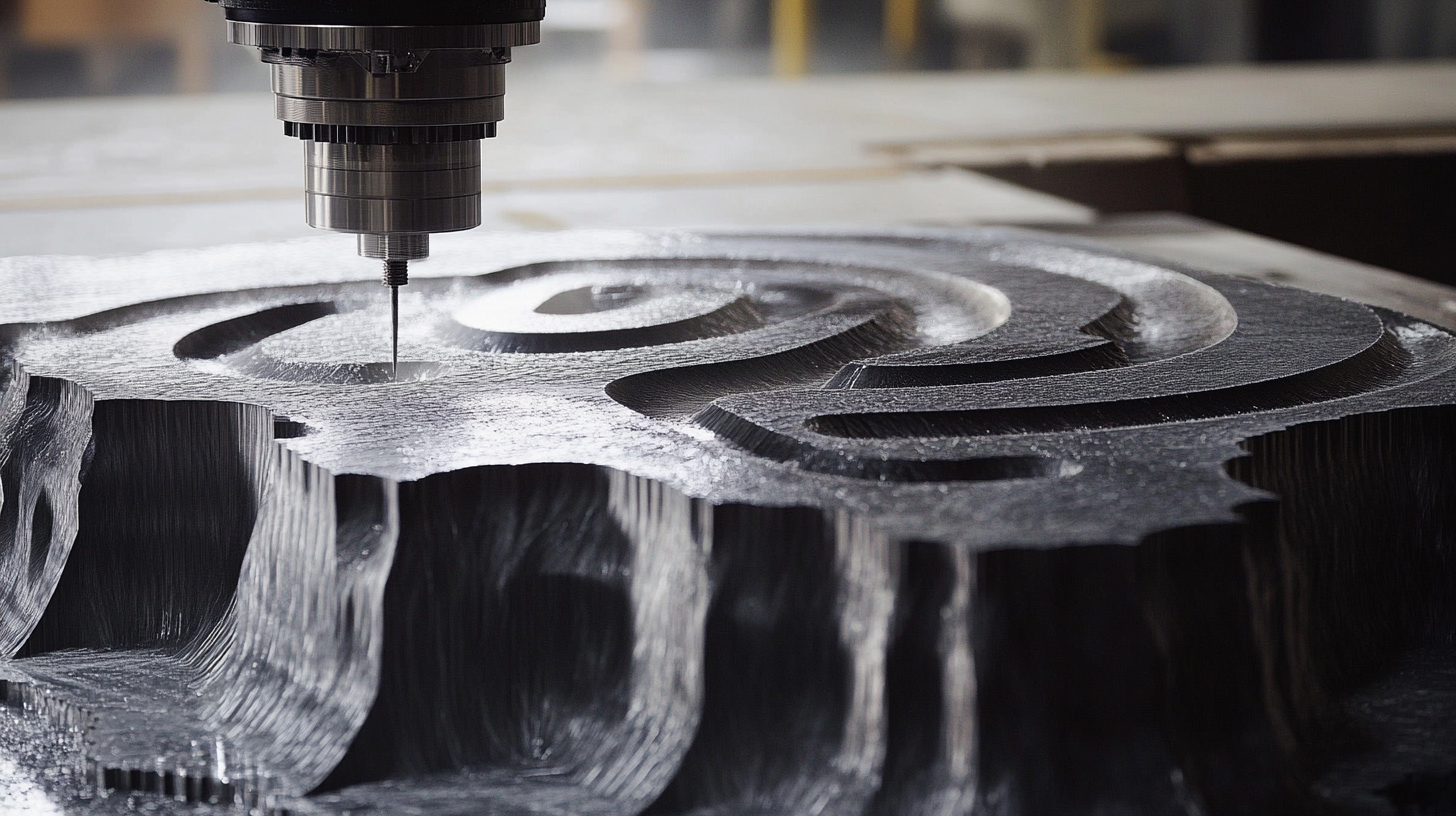
Market Analysis: The Impact of CNC Cutting on the Global Manufacturing Landscape
The CNC cutting industry is experiencing a transformative impact on the global manufacturing landscape, driven by advancements in technology and increasing demand across various sectors. As the backbone of many manufacturing processes, CNC machines enable precision and efficiency that are essential for producing high-quality products. With a projected market size of approximately $120.19 billion in 2024, the CNC machining and cutting market is set to witness substantial growth, driven by industries such as automotive, general machinery, and precision engineering.
Market analysis reveals that CNC cutting technologies are playing a pivotal role in the evolution of manufacturing. The growth trends in CNC tools indicate a short-term recovery, complemented by sustained long-term growth momentum. This is particularly evident as manufacturers increasingly adopt automation to improve productivity and reduce operational costs. Furthermore, the growth of the global CNC tools market is bolstered by innovations in conventional and CNC technologies, which provide enhanced capabilities, such as multitasking and greater customization options for clients.
In terms of regional performance, Asia-Pacific, particularly China, stands out as a leading market, projected to surpass $450 billion by 2025. This growth is fueled by rising industrial activities and significant investments in machinery upgrades. The CNC cutting market's impacts extend beyond the manufacturing sector, influencing trends in automation and robotics, as emerging technologies integrate into traditional processes, further reshaping the industry and its operational dynamics.
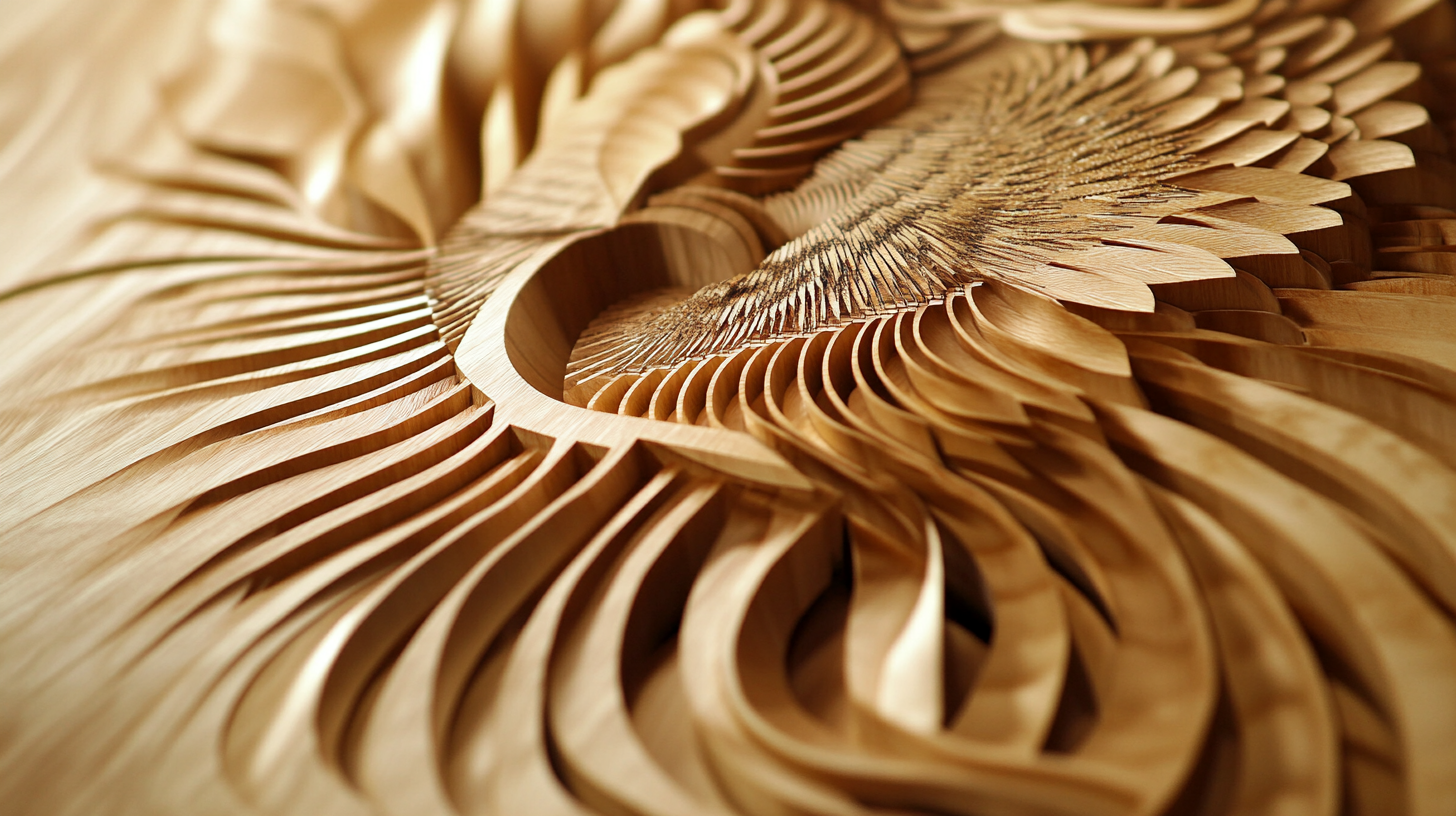
Diverse Applications of CNC Cutting: From Aerospace to Medical Devices
CNC cutting technology has made significant inroads across a multitude of industries, each benefiting from its precision and versatility. In the aerospace sector, CNC cutting plays a crucial role in the fabrication of complex parts that require stringent tolerances and lightweight characteristics. These components, such as turbine blades and structural frames, demand the accuracy that CNC machines provide, ensuring not only performance but also passenger safety.
In the medical device industry, CNC cutting further demonstrates its impact by enabling the production of intricate shapes and designs essential for advanced medical instruments. Devices such as surgical tools and implants necessitate a level of precision and customization that CNC cutting can deliver, thus advancing patient care and outcomes. The ability to rapidly prototype and manufacture these specialized components helps medical professionals innovate solutions tailored to individual patient needs.
Moreover, the emergence of hybrid manufacturing techniques, combining CNC cutting with 3D printing, is reshaping manufacturing processes. While 3D printing excels in creating complex geometries, CNC machining refines these parts to achieve superior surface finishes and tighter tolerances. This collaborative approach enhances productivity and offers manufacturers a wider range of fabrication options, making it easier to adapt to the fast-paced demands of various industries. As technology continues to evolve, the integration of CNC cutting with other methods will undoubtedly lead to even broader applications and innovations.
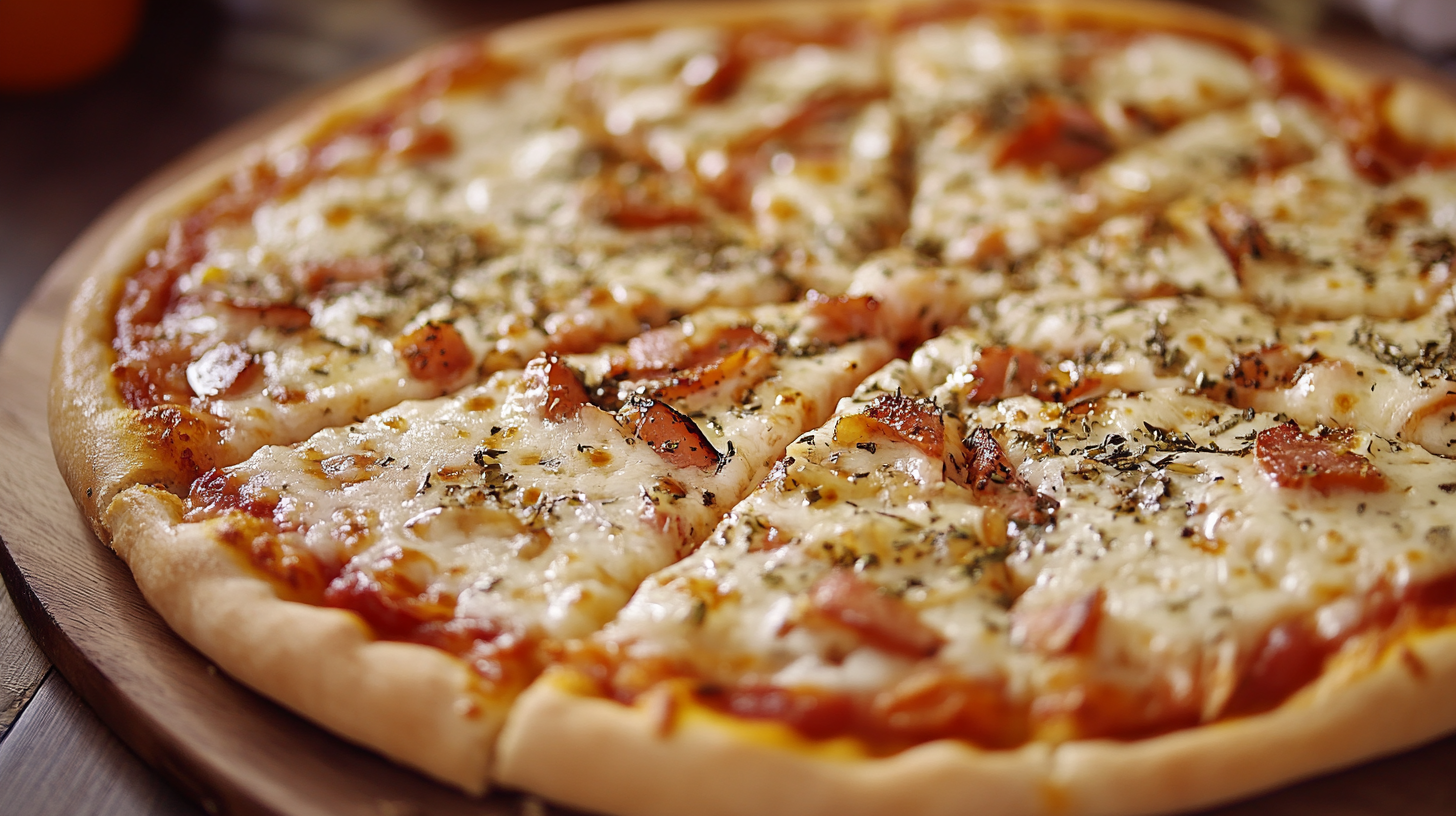
Efficiency and Precision: How CNC Cutting Enhances Production Processes
The CNC cutting industry has witnessed significant growth, with the global machine tool market projected to reach USD 110 billion by 2025, fueled largely by the demand for enhanced efficiency and precision across various sectors. CNC (Computer Numerical Control) cutting technology has become a cornerstone in production processes due to its ability to achieve high levels of accuracy and repeatability, which are essential in industries such as automotive, aerospace, and precision machinery. The ability to automate complex cutting tasks allows manufacturers to improve productivity metrics while minimizing waste—aligning with the industry's push toward lean manufacturing principles.
In the metal cutting segment alone, CNC cutting technology is expected to dominate, driven by its applications ranging from automotive components to general machinery. Notably, the precision offered by CNC technology supports the production of intricate parts that are indispensable in modern vehicles, thereby streamlining assembly processes and enhancing overall product quality. Industry reports highlight that CNC cutting machines are projected to account for over 60% of the market share in metal forming applications by 2024.
Regionally, North America and Europe are leading the way in CNC technology adoption, with a growing focus on smart manufacturing and Industry 4.0. As these regions invest in advanced machining solutions, they are expected to retain their dominance, while emerging markets in Asia-Pacific continue to display robust growth potential, supported by industrialization and increased foreign investment. Overall, the integration of CNC cutting within various industries exemplifies the transformative impact of technology on production efficiency and precision.
Future Trends in CNC Cutting: Innovations Shaping Industry Standards
The landscape of CNC cutting technology is evolving rapidly, driven by innovative advancements that redefine industry standards. A key trend emerging in this space is the integration of automation and precision engineering into CNC applications. This shift not only enhances the efficiency of metal cutting and forming processes but also addresses the growing demand for high-quality outputs across various sectors such as aerospace, automotive, and manufacturing.
As industries continue to embrace digital transformation, the advancements in CNC routers are particularly noteworthy. The introduction of features like auto-lubrication systems significantly decreases maintenance times, allowing businesses to optimize their operational efficiency. This level of automation not only streamlines production but also opens the door for smaller enterprises to enhance their capabilities and compete on a larger scale. Furthermore, the rising focus on precision cutting and advanced manufacturing is expected to spur continued growth in the CNC router market.
Education plays a vital role in this evolution, as evidenced by training programs designed to equip individuals with the essential CNC skills. Workshops focused on automation and programming are pivotal in meeting the employment needs of the industry, ensuring a skilled workforce ready to harness the power of modern CNC technology. As we look towards the future, innovations in CNC cutting are poised to further transform how industries operate, setting new benchmarks for quality and efficiency.