The Evolution of Precision in Cnc Fabric Cutting Technology
The landscape of fabric cutting has undergone a remarkable transformation with the advent of CNC fabric cutting technology. This evolution has significantly enhanced precision and efficiency, which are crucial in today's fast-paced manufacturing environment. At the forefront of this innovation is the CNC fabric cutting machine, a tool that has revolutionized the way fabrics are processed. By utilizing advanced software and automation capabilities, these machines minimize human error and maximize material utilization, leading to both cost savings and enhanced production speed. As the textile industry continues to embrace technological advancements, the importance of precision in cutting fabrics becomes ever more evident. This blog will explore the journey of CNC fabric cutting technology, highlighting its development, current capabilities, and the future trends that promise to further enhance its precision and efficiency.
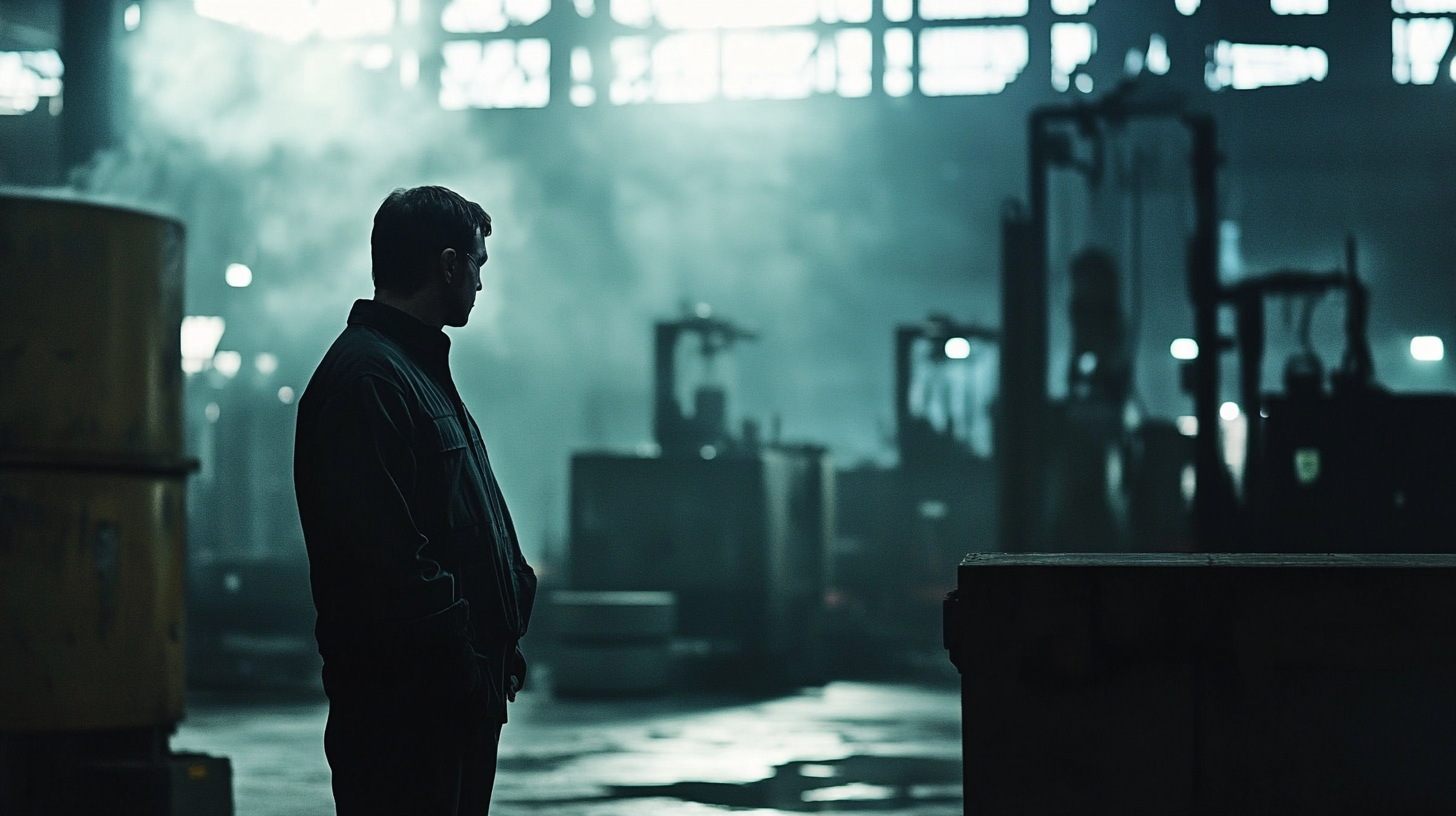
The Historical Context of CNC Fabric Cutting Technology Development
The history of CNC fabric cutting technology dates back to the 1950s when the demand for precision in manufacturing began to rise. Initially, fabric cutting was a labor-intensive process, involving manual tools that often led to inconsistencies in cut quality. The introduction of computerized numerical control (CNC) systems revolutionized this sector by allowing for automated, precise cutting paths based on digital designs. According to a report by Markets and Markets, the global CNC machine market is expected to reach $117.2 billion by 2026, reflecting the growing reliance on precision technology across various industries, including textiles.
As time progressed, advancements in software and hardware further enhanced CNC fabric cutting capabilities. The late 1990s saw the advent of CAD (Computer-Aided Design) and CAM (Computer-Aided Manufacturing) integration, allowing for seamless transition from design to production. A study from Technavio predicts that the fabric cutting machine market will grow at a CAGR of over 6% during 2021-2025, highlighting the continuous evolution in this technology. This growth can be attributed to the increasing customization demands in fashion and manufacturing, necessitating accurate cutting processes to maintain competitive advantage in a rapidly evolving market.
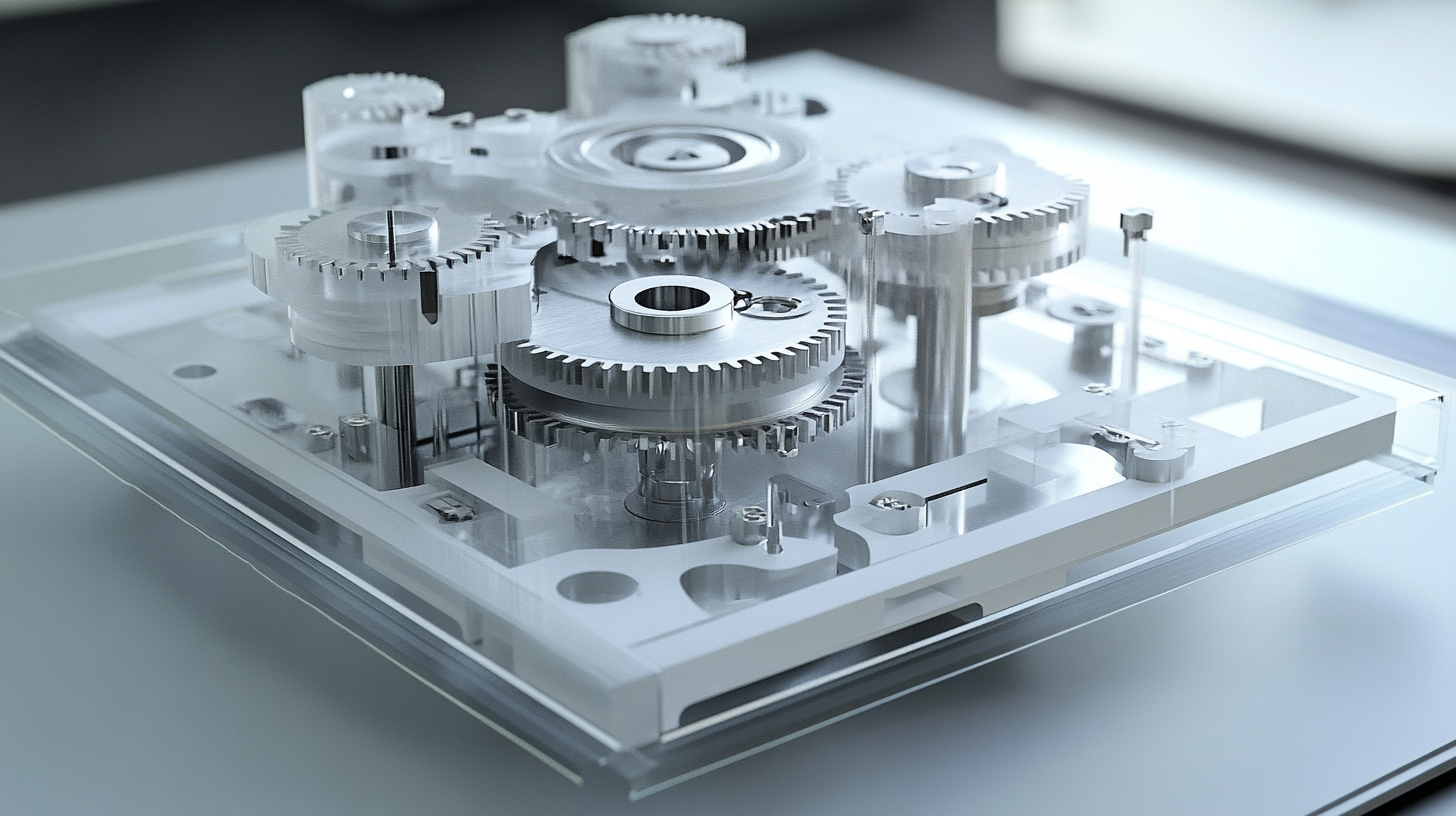
Key Innovations That Shaped Precision in CNC Fabric Cutting Machines
CNC fabric cutting technology has undergone significant evolution over the years, driven by key innovations that have dramatically enhanced precision and efficiency. One of the most pivotal advancements has been the incorporation of advanced computer algorithms. These algorithms enable CNC machines to execute intricate cutting patterns with remarkable accuracy, minimizing fabric waste and ensuring precise adherence to design specifications. By utilizing sophisticated software, operators can easily adjust parameters and optimize cutting sequences, leading to a smoother workflow and higher-quality end products.
Another groundbreaking innovation is the development of laser cutting technology. Lasers provide a level of precision that traditional cutting methods cannot match. The focused beam of light cuts through fabric with a clean finish, eliminating the need for additional finishing processes. This not only speeds up production times but also improves the overall quality of the fabric edges, reducing fraying. Additionally, the integration of automation and AI in CNC machines allows for real-time adjustments and monitoring, further enhancing precise cutting capabilities while reducing human error. These technological advancements are crucial for businesses aiming to meet the demands of custom fabric designs while maintaining high standards of precision.
The Evolution of Precision in CNC Fabric Cutting Technology
Year | Innovation | Impact on Precision | Key Manufacturers |
---|---|---|---|
1970s | Introduction of CNC Technology | Enhanced cutting accuracy and repeatability | Gerber, Lectra |
1980s | Laser Cutting Integration | Allowed for intricate designs with high precision | Fabricsystems, Trotec |
1990s | Software Advancements | Improved design-to-cut workflows, reducing errors | Optitex, Gerber Technology |
2000s | 3D CAD and Simulation | Enabled precise visualizations before cutting | Autodesk, SolidWorks |
2010s | Automation and IoT Integration | Real-time monitoring and adaptive cutting techniques | Dürkopp Adler, Zünd |
Current Industry Standards and Specifications for CNC Cutting Accuracy
The precision of CNC fabric cutting technology has become increasingly critical in meeting the demands of various industries, particularly in apparel and upholstery. Current industry standards emphasize that accuracy is paramount, with specifications often reaching tolerances as fine as ±0.1 mm in advanced CNC systems. According to a recent report by the American Association of Textile Chemists and Colorists, the need for precision in fabric cutting can significantly reduce material waste, enhancing both efficiency and cost-effectiveness in production processes.
Moreover, advancements in software and machine calibration have played a crucial role in improving cutting accuracy. As reported by the International Textile Manufacturers Federation, a staggering 70% of manufacturers now utilize sophisticated CAD/CAM systems to optimize their cutting processes. These systems not only allow for precise measurement and pattern layouts but also integrate with real-time monitoring to ensure that every cut meets the necessary specifications. This level of accuracy not only streamlines production but also ensures that the final products align perfectly with design intents, further solidifying the importance of precision in CNC fabric cutting technology.
Impact of Material Properties on CNC Cutting Precision and Efficiency
The precision of CNC fabric cutting technology has progressed significantly over the years, driven in part by a deeper understanding of material properties. When dealing with various fabrics—be it woven, non-woven, or knit—each material exhibits unique characteristics that can influence cutting outcomes. For instance, the thickness, elasticity, and weave of a fabric can affect how well it is held in place during the cutting process. This has led manufacturers to adapt their CNC systems to compensate for these variations, ensuring consistent precision regardless of the material used.
Furthermore, the efficiency of CNC cutting is closely tied to the method of operation employed, which needs to be tailored to the specific fabric properties. Advanced algorithms and sensors are now able to analyze the material in real-time, allowing for adjustments in cutting speed, pressure, and tool path. As a result, manufacturers can optimize their processes, reducing waste while enhancing the quality of the cut. Investing in CNC technology that accounts for material behavior not only improves precision but also boosts overall operational efficiency, making it an indispensable aspect of modern fabric cutting practices.
Future Trends: Advancements in CNC Technology and Their Implications for Fabric Cutting
The advancements in CNC technology are revolutionizing fabric cutting, promising a future characterized by unprecedented precision and efficiency. According to recent reports, the CNC cutting machines market is projected to reach USD 11,671.4 billion by 2032, driven primarily by the rising demand for automation and high accuracy in manufacturing processes. This growth signifies a fundamental shift in how fabric is cut, enabling manufacturers to produce intricate designs with minimal waste.
As part of this evolution, the integration of AI in CNC machining is expected to have a significant impact. For instance, the global 5-axis CNC machining centers market is anticipated to grow by USD 792.5 million between 2024 and 2028, highlighting the shift towards self-optimized machine cutting that leverages artificial intelligence. This cutting-edge technology not only enhances operational efficiency but also adapts to various material types and patterns, setting the stage for smarter fabric cutting solutions in the textile industry.
Moreover, the recent surge in machine tool orders indicates a robust demand for capital equipment, particularly in metal-cutting and forming sectors. U.S. manufacturers have shown increased investment in CNC technologies that promote innovation and productivity. This trend underscores the importance of precision and technological advancement in maintaining competitiveness in the fabric cutting market, paving the way for future developments that prioritize both efficiency and sustainability.
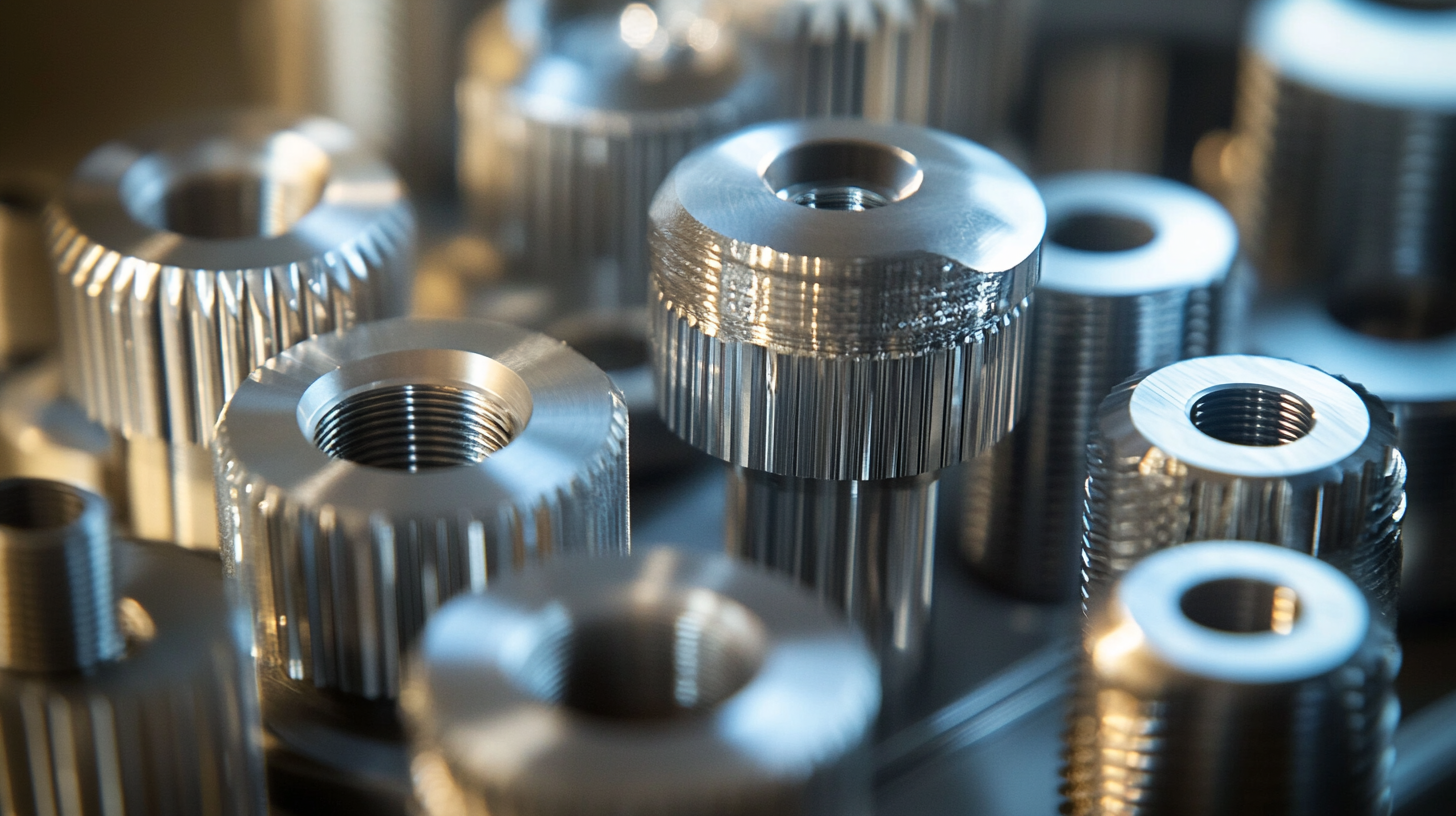